The integration of robotics, Autonomous Underwater Vehicles (AUVs), and Real-Time Sensors and Analytics in remote, underwater oil operations is emerging as a viable way enhance efficiency, safety, and sustainability in offshore drilling. In this EDI feature, we will explore how robotics is rapidly changing the offshore industry and the key challenges to their widespread development.
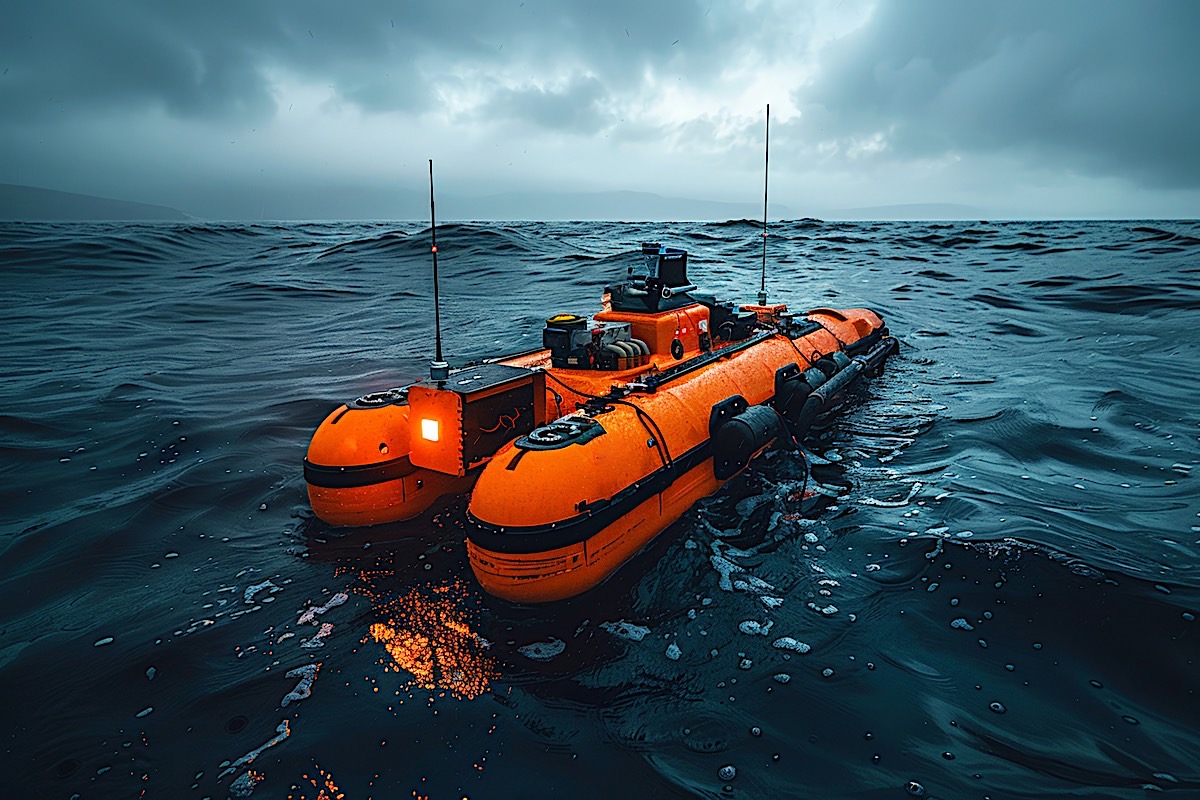
Real-Time Automated Operational Efficiency
One of the most significant advantages of incorporating robotics and remote operations into offshore drilling is the potential for improved operational efficiency. Robotics can automate repetitive tasks, allowing for more precise and consistent execution of drilling processes.
Remote monitoring systems, especially when used with robotics, enable real-time data analysis, leading to quicker decision-making and problem-solving.
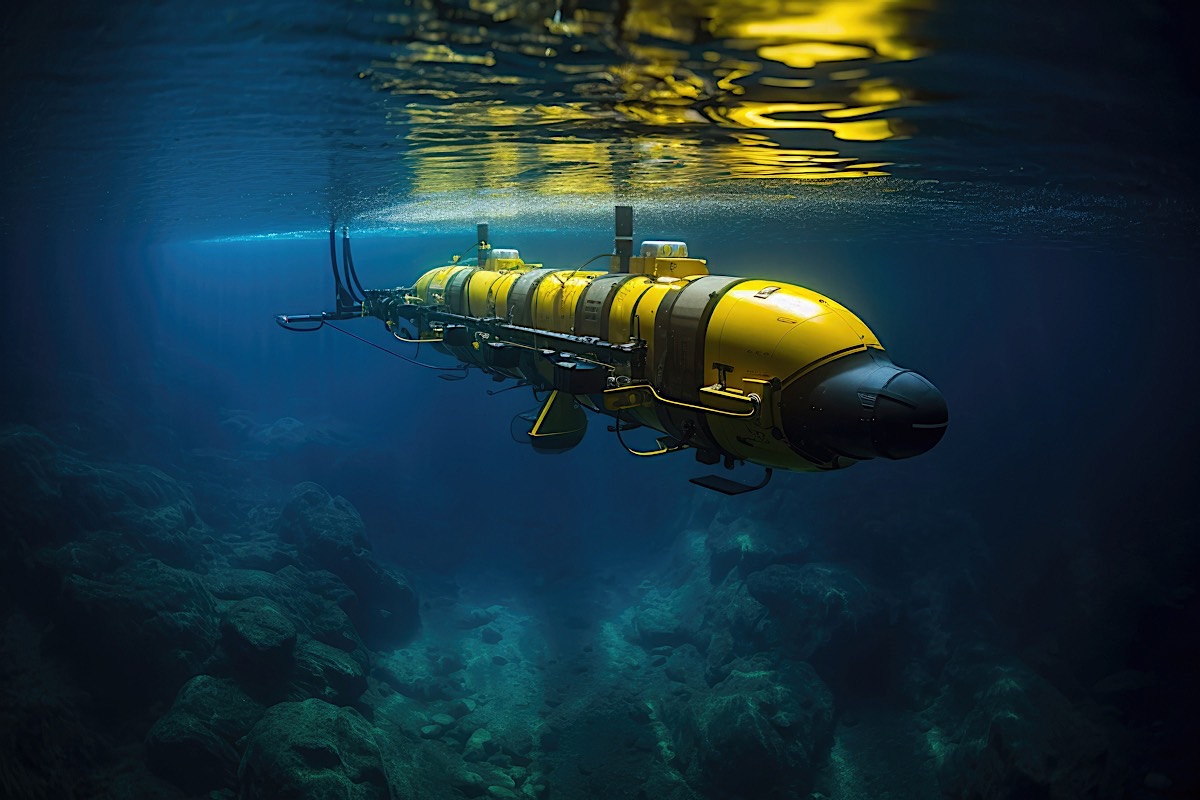
The use of autonomous underwater vehicles (AUVs) can facilitate inspections and maintenance tasks that would traditionally require human divers, reducing downtime and operational costs and increasing safety. Advanced data analytics can optimize drilling parameters, resulting in higher production rates.
Case: Stereo Vision Automois ORB-SLAM3
ORB-SLAM3 is effective and robust enough for UAV self-localisation, and the developed stereo vision-based autonomous navigation approach can be deployed for pressure vessel visual inspection. This overcomes some of the main issues with remote monitoring and exploration.
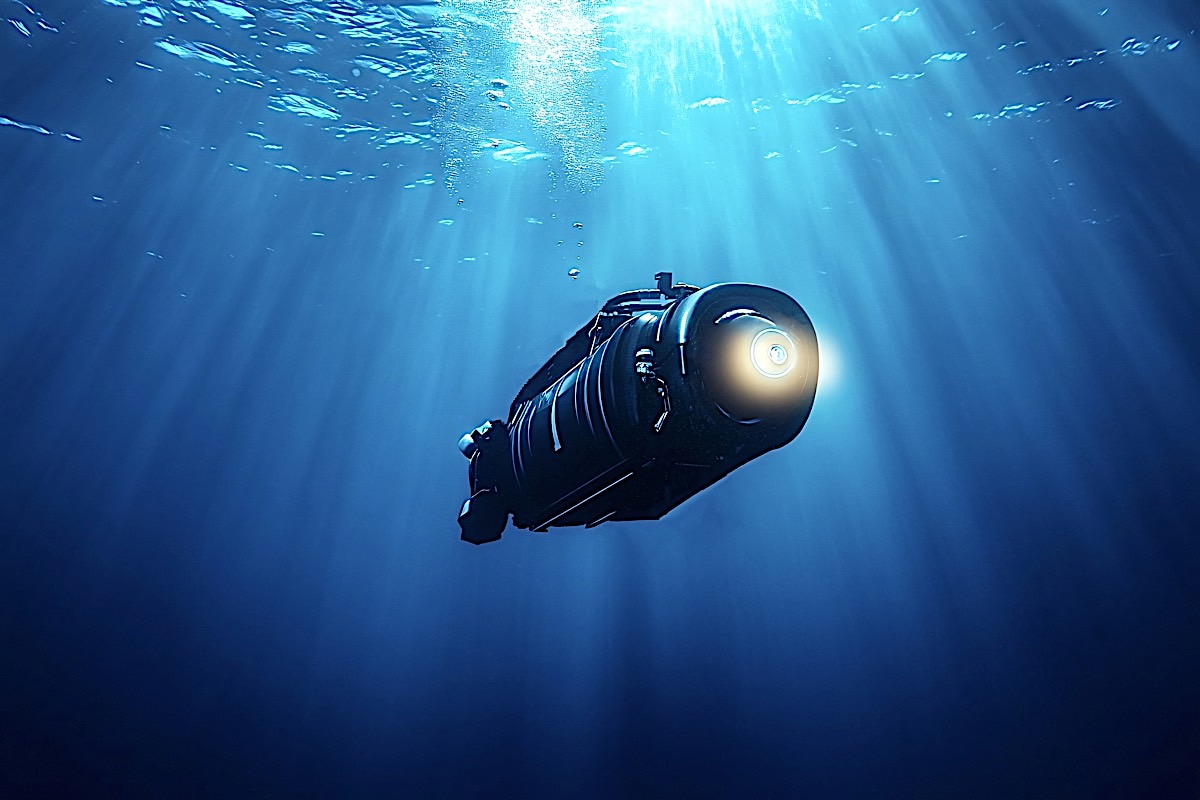
As explained in a paper by Leijian Yu, Erfu Yang and Beiya Yang:
“It is vital to visually inspect pressure vessels regularly in the oil and gas company to maintain their integrity. Compared with visual inspection conducted by sending engineers and ground vehicles into the pressure vessel, utilising an autonomous Unmanned Aerial Vehicle (UAV) can overcome many limitations including high labour intensity, low efficiency and high risk to human health.”
By streamlining operations and reducing the need for human intervention in hazardous environments, robotics and remote operations enhance productivity and the operational framework of offshore drilling.
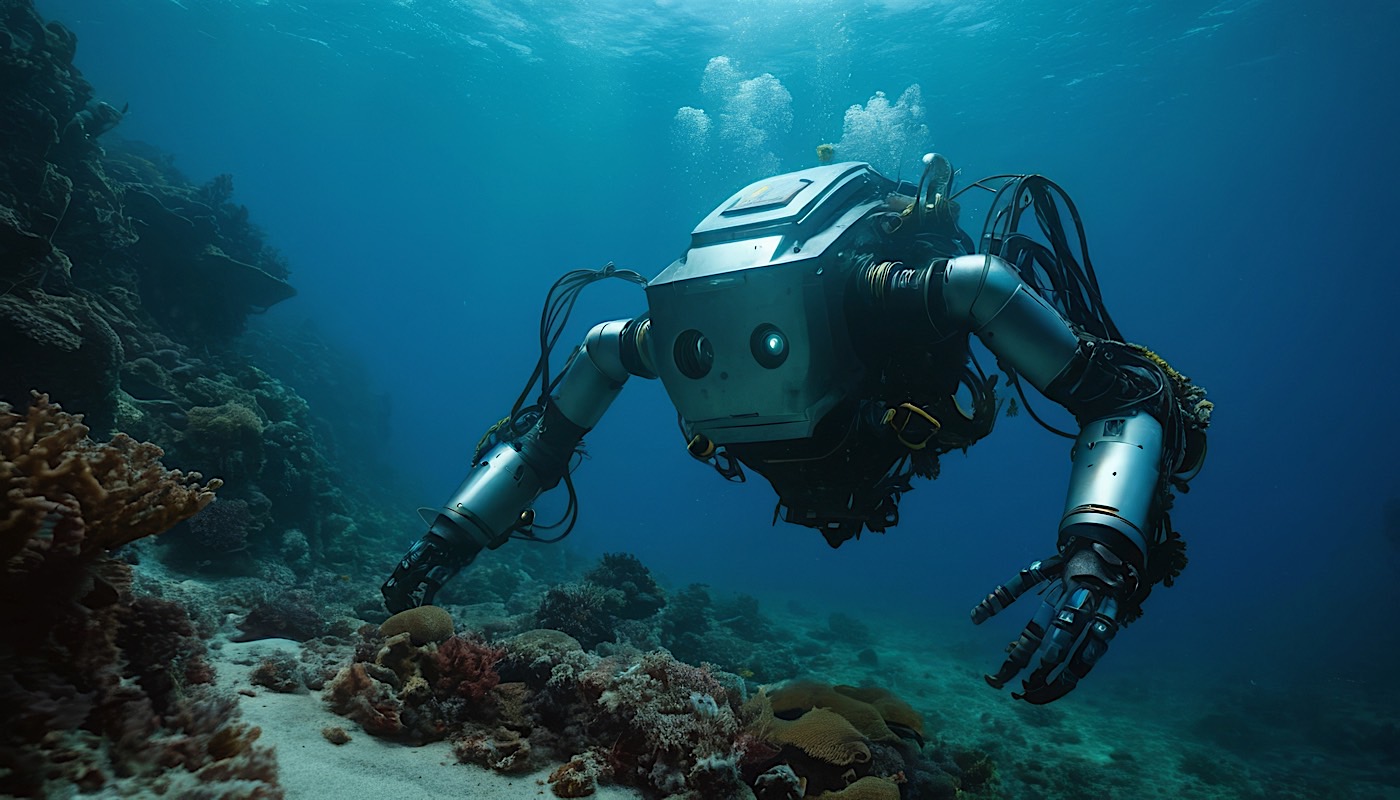
Enhanced Safety Measures
Safety is a paramount rationale in offshore oil drilling, where the risks associated with human error and environmental hazards are significant and even life-threatning. The implementation of robotics and remote operations can substantially mitigate these risks. Robotics can take on dangerous tasks, reducing the potential for accidents and injuries among workers.
Typically, the concept is for robotic systems to handle dangerous materials or perform inspections in high-risk areas, such as blowout preventers and subsea wellheads. Remote monitoring technology allows for continuous oversight of drilling operations, enabling rapid responses to potential emergencies.
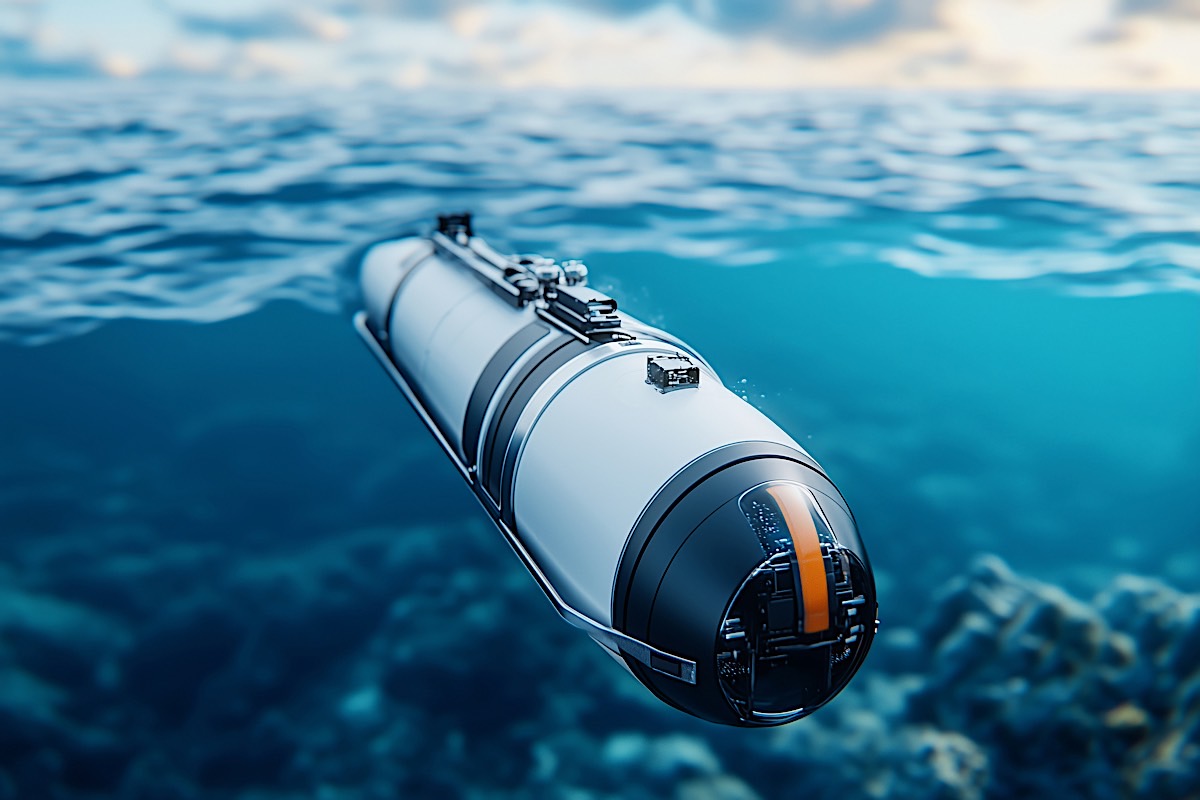
Minimizing Environmental Impacts
As environmental concerns become increasingly prominent, the offshore oil drilling industry faces pressure to adopt more sustainable practices. Robotics and remote operations offer innovative solutions to minimize the ecological footprint of drilling activities. These technologies can enhance environmental monitoring and reduce the likelihood of spills and other accidents.
For example, one control system for path following, and algorithms for obstacle detection and avoidance, are presented for a USR with thrusters attached at the tail module, thereby providing intervention capabilities which exceed those of AUVs and inspection class ROVs.
E. Kelasidi, Signe Moe, K. Pettersen in the abstract describing this system wrote:
“The use of unmanned underwater vehicles is steadily increasing for a variety of applications such as mapping, monitoring, inspection and intervention within several research fields and industries, e.g., oceanography, marine biology, military, and oil and gas. Particularly interesting types of unmanned underwater vehicles are bio-inspired robots such as underwater snake robots (USRs). Due to their flexible and slender body, these versatile robots are highly maneuverable and have better access capabilities than more conventional remotely operated vehicles (ROVs). Moreover, the long and slender body allows for energy-efficient transit over long distances similar to torpedo-shaped autonomous underwater vehicles (AUVs).”
Some other applications include drones equipped with sensors can monitor air and water quality in real-time, allowing for immediate detection of any anomalies. Going beyond monitoring, precision drilling techniques could be facilitated by robotics and reduce the amount of waste generated during operations.
Transforming Offshore Remotely
At the bleeding edge of the technologies are even radical new models of robotic motion. One journal paper analyzes the viability of a snake-like robot system. Explains E. Kelasidi et al in “Experimental investigation of efficient locomotion of underwater snake robots for lateral undulation and eel-like motion patterns”:
“…of swimming snake robots by presenting and experimentally investigating fundamental properties of the velocity and the power consumption of an underwater snake robot for both lateral undulation and eel-like motion patterns and investigates the relationship between the parameters of the gait patterns, the forward Velocity and the energy consumption for different motion patterns.”
As the oil industry adopts or adapts to these technologies, it will be essential to consider the implications, including the need for workforce retraining and the ethical concerns surrounding automation. Ultimately, the successful implementation of these technologies will not only redefine offshore drilling practices but also contribute to a more sustainable energy future and a safer work environment.