The ongoing global microchip shortage has significantly impacted various industries, with the automotive sector being hit particularly hard. Assembly plants in North America and Europe have faced production cutbacks, resulting in millions of vehicles being cut from production schedules. This crisis has forced automakers to adapt and seek new opportunities, including pivoting to electric vehicles and exploring in-house chip production.
In this article, we’ll delve into the challenges faced by the automotive industry due to the microchip shortage and discuss the potential opportunities for innovation that have arisen as a result.
Impact of Microchip Shortage on the Automotive Industry
The microchip shortage has had a significant impact on vehicle production schedules, primarily in North America and Europe, which represent the majority of cutbacks worldwide. According to AutoForecast Solutions[1], North American assembly plants have cut 29,315 vehicles out of their schedules, while European manufacturers have dropped 15,096 in a week. This shortage has led to a projected 2.8 million global vehicle cuts for the year 2023, a staggering number that underscores the severity of the problem.
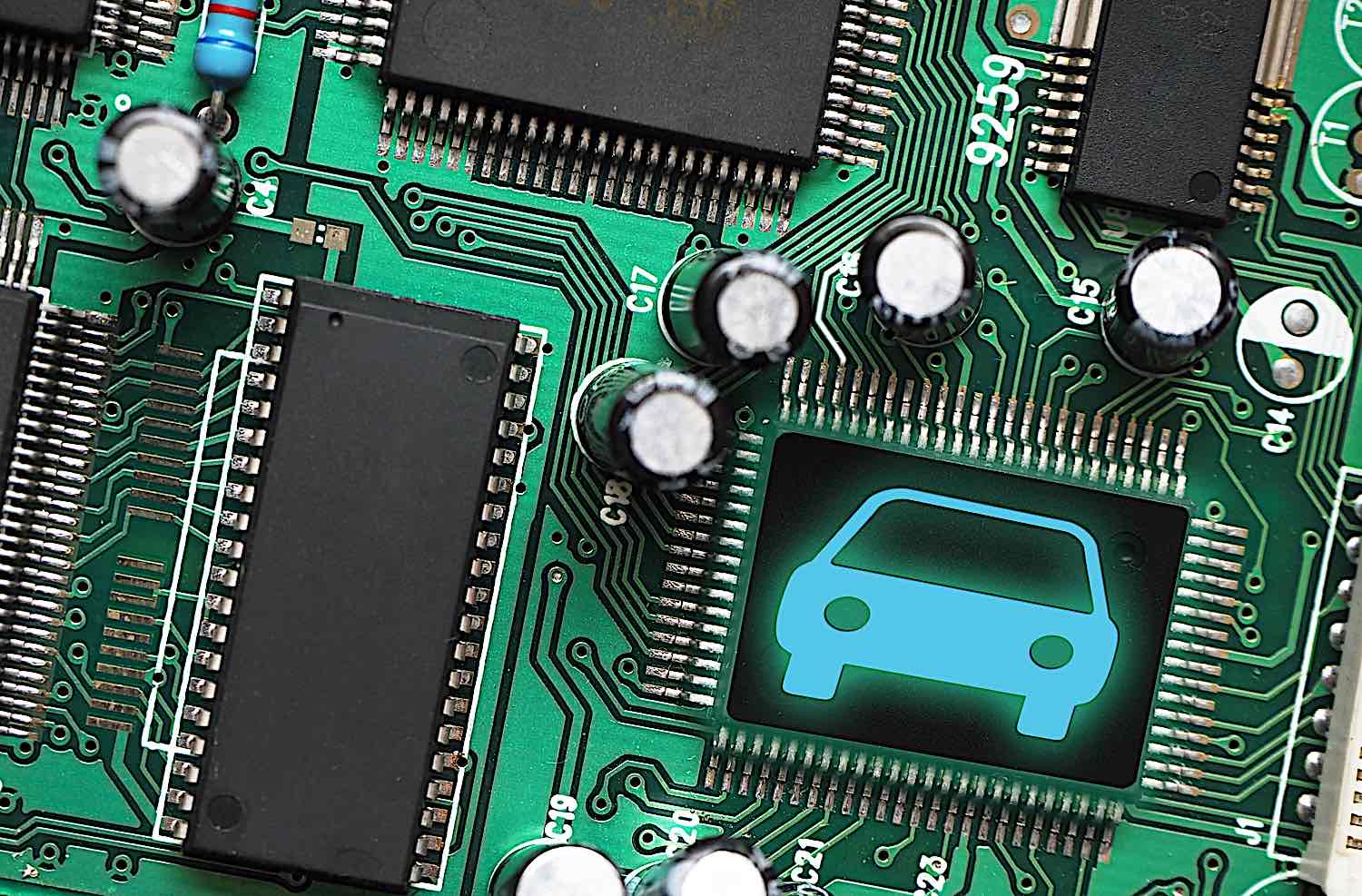
Automakers were caught off guard by the sudden surge in demand for microchips by other industries, such as consumer electronics, during the pandemic[2]. As people worldwide were confined to their homes, the demand for gadgets like gaming consoles, TVs, and home appliances skyrocketed, leading manufacturers to increase their chip requirements. In contrast, the automotive industry initially scaled back their orders, expecting a prolonged slump in car sales. This created a supply chain imbalance, with automotive manufacturers struggling to source enough microchips for their vehicles.
A modern car can contain more than 3,000 microchips, which control essential functions such as brakes, doors, airbags, and advanced driver assistance systems[3]. The shortage of these critical components has forced automakers to adjust their production strategies and make difficult decisions regarding which models and features to prioritize. The microchip shortage has also had ripple effects on suppliers, dealers, and consumers, leading to longer wait times for new vehicles, reduced availability of certain models, and increased prices in some cases.
The ongoing microchip shortage has exposed the vulnerabilities of the automotive industry’s supply chain and highlighted the need for more robust risk management strategies. Automakers must now reconsider their reliance on just-in-time manufacturing practices, which prioritize efficiency and cost reduction but can leave them exposed to supply chain disruptions.
Additionally, the crisis has shown the importance of having a diversified supply chain and strong relationships with key suppliers, as well as the need to invest in alternative technologies and materials that can help mitigate the impact of future shortages.
Strategies Adopted by Automakers During the Shortage
Faced with the microchip shortage, automakers have had to make difficult decisions to minimize the impact on their production lines. One approach taken by automakers was to prioritize the allocation of scarce microchips for their more expensive and higher-margin models. General Motors, for example, opted to hoard microchips for their premium vehicles while temporarily shutting down factories producing lower-priced sedans[4]. This allowed them to maintain production levels for their most profitable models despite the supply chain constraints.
Another strategy adopted by automakers involved removing features that relied heavily on microprocessors. BMW, for instance, eliminated parking assistance and touchscreen capabilities in some models to save on chip usage. Similarly, Mercedes-Benz removed high-end audio systems and wireless phone charging from some vehicles to conserve their supply of microchips[5]. By selectively removing non-essential features, automakers were able to continue production with fewer chips, albeit with reduced functionality.
In response to the semiconductor shortage, some automakers have also shifted their focus towards electric vehicles (EVs). While EVs still require microchips, the transition to electric powertrains can help address certain supply chain issues and reduce dependency on traditional microchips.
Furthermore, as governments around the world implement stricter emissions regulations, investing in electric vehicles can prove to be a strategic move for automakers. By pivoting towards EV production, companies can stay ahead of the curve and position themselves for future growth in an increasingly electrified market.
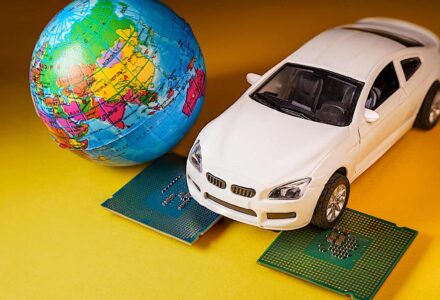
Opportunities for Innovation and Collaboration
The microchip shortage has revealed vulnerabilities in the automotive industry’s supply chain and the need for increased collaboration between automakers and chip manufacturers. One opportunity for innovation and collaboration is the development of in-house expertise in chip design and production, which can reduce dependency on suppliers. Ford’s collaboration with US chipmaker GlobalFoundries serves as an example of this approach.
Another opportunity lies in building direct relationships with chip manufacturers. By engaging with chipmakers directly, automakers can have more control over their supply chain and better anticipate potential disruptions. This can help ensure a steady flow of microchips and alleviate supply chain bottlenecks.
Embracing electric vehicle, technology also presents an opportunity for automakers to innovate and develop new technologies that rely less on traditional microchips, helping to reduce the impact of future shortages. As the industry shifts towards electric vehicles, companies can explore alternative technologies and materials to mitigate the reliance on microchips.
Lastly, traditional automakers can learn from industry disruptors such as Tesla, BYD, and NIO, which have extensive operations dedicated to designing or producing their own chipsets. By studying and adapting the strategies of these self-sufficient carmakers, traditional automakers can better prepare themselves for future supply chain challenges and ensure long-term resilience in the face of unforeseen disruptions.
Future Outlook and Lessons Learned
As the automotive industry continues to grapple with the microchip shortage, it is crucial to look ahead and consider the future outlook for both the industry and the semiconductor supply chain. The lessons learned from this crisis can provide valuable insights for automakers and help them better prepare for potential disruptions in the future.
One of the key takeaways from the microchip shortage is the importance of supply chain resilience. The automotive industry must work towards diversifying its sources of critical components, such as microchips, to avoid over-reliance on a single supplier or region. This diversification can involve building relationships with multiple suppliers, investing in localized production, or developing strategic partnerships with key players in the semiconductor industry.
Another lesson learned is the need for greater collaboration between automakers and semiconductor manufacturers. This collaboration can help ensure a more transparent and efficient supply chain, allowing both parties to anticipate demand fluctuations better and allocate resources accordingly. To achieve this, automakers should establish direct lines of communication with chipmakers, share forecasting data, and collaborate on research and development efforts to drive innovation in semiconductor technology.
Furthermore, the microchip shortage has underscored the importance of investing in research and development to explore alternative technologies and materials that can help mitigate the impact of future shortages. For example, the ongoing shift towards electric vehicles[6] presents an opportunity for automakers to innovate and develop new technologies that rely less on traditional microchips. By investing in these areas, the automotive industry can work to reduce its dependency on semiconductors and build a more resilient supply chain for the future.
Lastly, the crisis has highlighted the need for automakers to stay agile and adaptive in the face of unforeseen challenges. This can involve implementing flexible production strategies that allow for rapid adjustments in response to supply chain disruptions, as well as investing in digital transformation initiatives to improve visibility and control across the entire supply chain.
Key Takeaways
The ongoing microchip shortage has exposed the vulnerabilities in the automotive industry’s supply chain and emphasized the need for automakers to rethink their strategies and focus on innovation. By investing in in-house expertise, forging stronger relationships with chip manufacturers, and embracing new technologies such as electric vehicles, automakers can mitigate the impact of future shortages and ensure their resilience in an increasingly competitive market.
Lessons learned from the microchip shortage, such as the importance of supply chain resilience, greater collaboration, investing in research and development, and staying agile in the face of challenges, should be taken to heart by the automotive industry. These insights provide valuable guidance for addressing current and future supply chain disruptions.
The automotive industry must view the microchip shortage as a wake-up call, pushing them to adapt, innovate, and strengthen their supply chains to meet the demands of an ever-evolving technological landscape. By proactively addressing the challenges brought on by the microchip shortage and applying the key takeaways outlined in this report, the industry can emerge more robust and better prepared for future disruptions.
Sources:
[1] The latest numbers on the automotive microchip shortage | Automotive News Canada (autonews.com)
[2] Why Is There a Chip Shortage? Covid-19, Surging Demand Cause Semiconductor Shortfall (bloomberg.com)
[4] General Motors Set to Fight Chip Shortage With Its Own Microchips by 2025 – autoevolution
[5] Will the Chip Shortage End in 2023? Here’s What Experts Say (automoblog.net)
[6] How countries are encouraging the move to electric cars | World Economic Forum (weforum.org)