This fall, a prototype of a new concept, in passenger or cargo jets may lead to substantial fuel savings — expected to be at least 20 percent, and emissions by up to 35 percent.
Developed conceptually by student Justus Benad, the entire body fuselage is a flying wing, pushing passengers into the wings for ultimate aerodynamic efficiency.
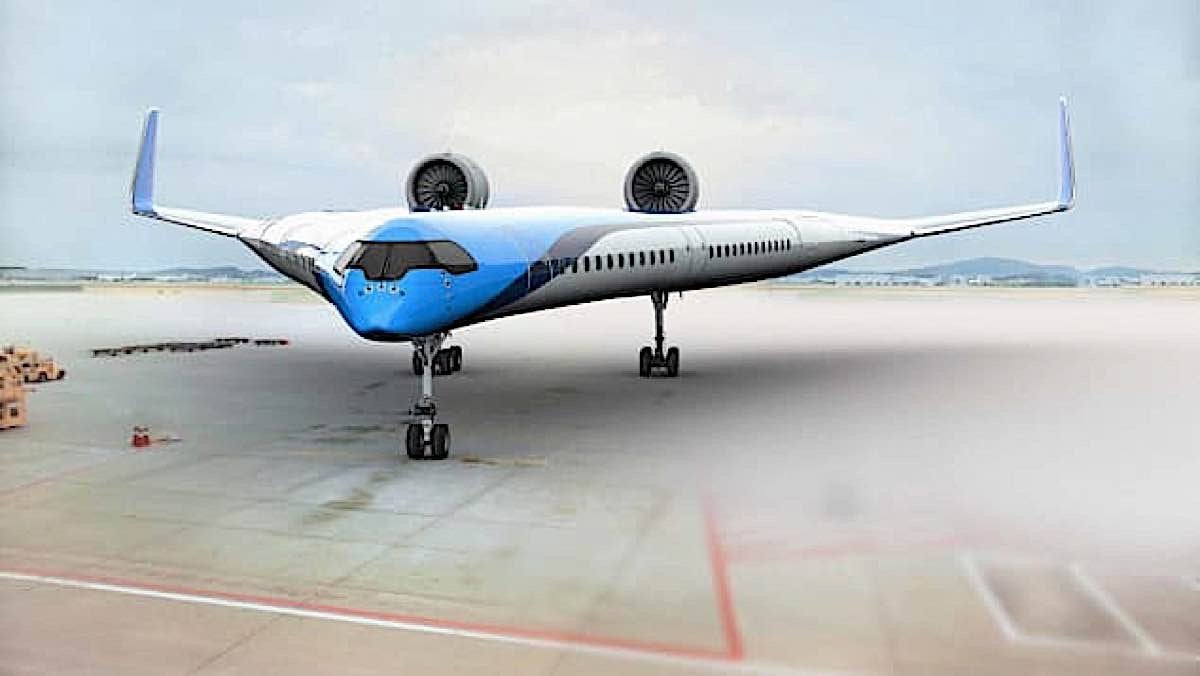
In the past, flying wing designs have supported large payloads at high altitudes, notably in the military craft. Here, the concept of Justus Benand of Berlin’s Technical University is to create the most efficient shape and lightest relative weight ratio.
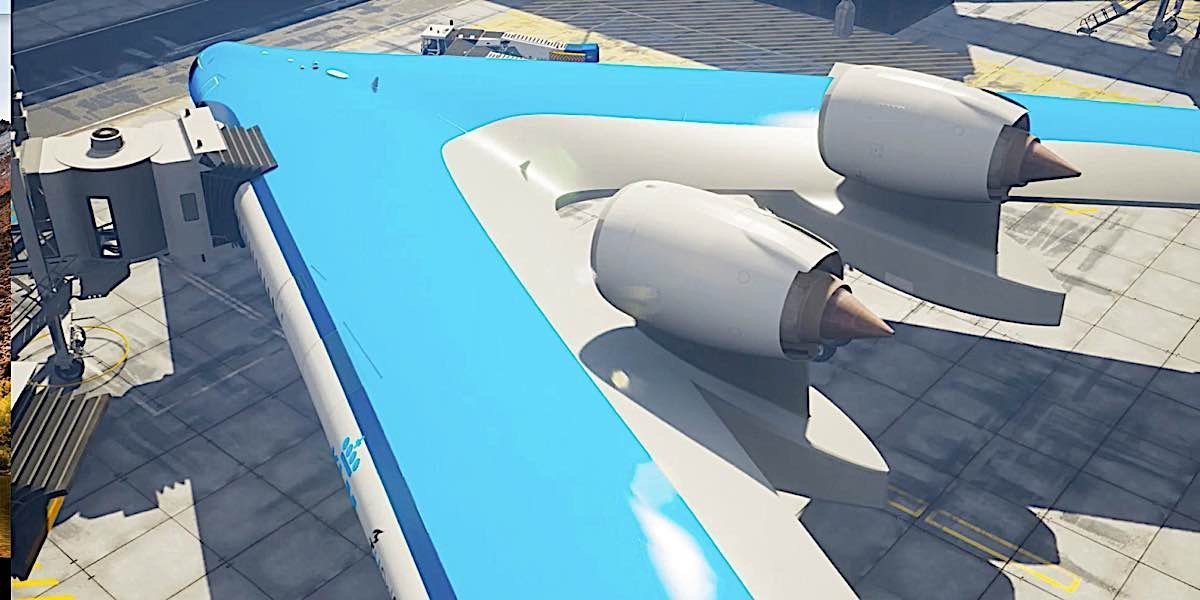
Moving to prototype possibly this fall (2019) — as developed further by Delft Technical University in the Netherlands, working with KLM’s Dutch airline — the flying V design is substantially lighter than normal airframes with wings. Typically, modern jets only use the wings for engines and fuel tanks.
With the flying wing, passengers, fuel and cargo will all be integral to the “wing” fuselage, with the twin engines moving to the rear of the V-Wing and a notable absence of traditional vertical stabilizer in the centre — moved, in this design, to the tips of each wing.
On aircraft, vertical stabilizers almost always point upwards. For this reason these are also known as the vertical tail, and are part of an aircraft’s empennage. With the flying wing, a “tail” may no longer be appropriate. The upright mounting positions has two major benefits with drag of the stabilizer increasing at speed — which can create a nose-up moment that helps to prevent dangerous overspeed; and, sccondly, for banking (turning), the stabilizer produces lift which counters the banking moment. This area of the new design, with twin vertical stabilizers on the tips of each wing, will require extensive testing.
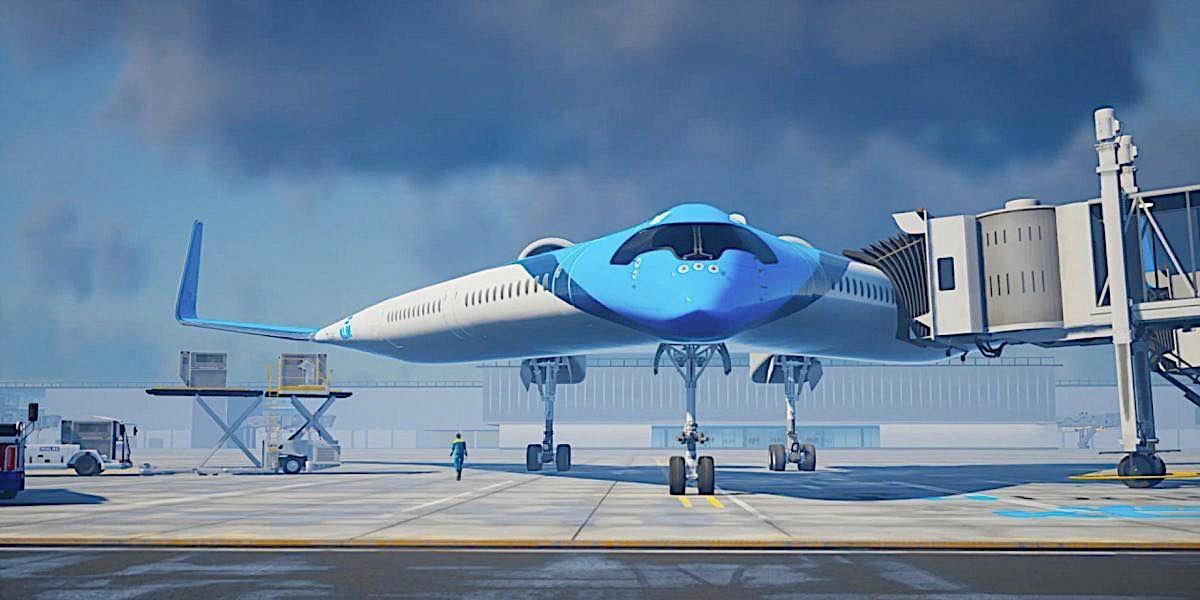
In design and wind tunnel tests, the design is near-optimal, with a projected efficiency gain of 20 percent over today’s most advanced A350 design.
Overall, the flying wing has less “resistance” resulting in less fuel to propel the relative weight. Although the design is efficient, the main issue to be tested in the prototype is stability at various speeds.
Depending on tests, working models of the “flying wing” may not make production for many years.
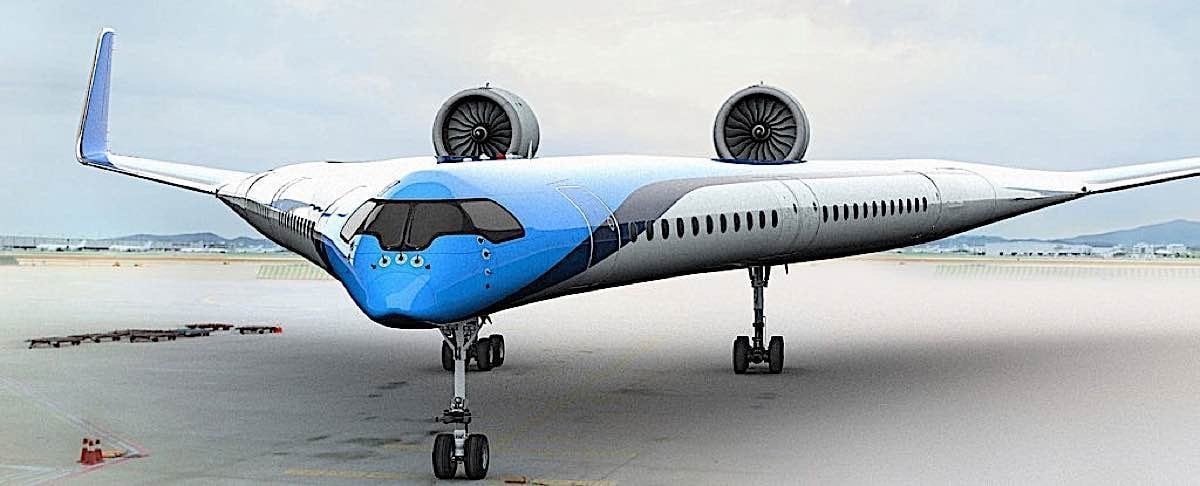