Evolutionary advancements in drilling technology — for example ultrashort pulsed fiber-based lasers or fuzzy-ball fluid — are making traditional practices more sophisticated, especially when driven by real-time data analytics.
Automated drilling rigs and real-time data analytics are key developments that enhance operational efficiency and even promote safety and the all-important environmental stewardship mandates of today. In this special EDI feature, we explore the implications of the latest technological breakthroughs in drilling practices, focusing on their impact on productivity, cost-effectiveness, and risk management.
Linking these various emerging innovations are data-analytics automation that maximize efficiency, capacity, wear-and-tear and safety.
Quick Facts: Emerging Innovations
- Application of a specialized fluid known as “Fuzzy-ball” fluid: Fuzzy-ball fluid has been discovered to bolster a formation’s pressure-bearing capabilities and systematically augment resistance against oil, gas, and water flow.
- Various Process Systems Engineering (PSE) methodologies a drastic departure from ad hoc/one-use tools and methods of the past.
- Applied Hydro-aeromechanics in Oil and Gas Drilling offers a unique resource for properly modeling and understanding the hydro-dynamic forces affecting a drilling site.
- Several studies have examined the use of various types of nanoparticles (NPs) as additives to enhance the properties and improve the performance of the drilling fluid to mitigate the drilling problems.
- Advanced data analytics for reservoir management, IoT sensors for equipment monitoring, and algorithms for optimizing production processes.
- Various cementing processes used in ultra-deep well development
Evolution of Drilling Technology
The evolution of drilling technology advanced the automation of rigs, enabling efficient systems capable of operating with less human error and higher safety and cost-benefits. This is driven by the integration of digital technologies automation, plus real-time data, enhancing operational efficiency and safety in drilling processes.
The implementation of intelligent sensing technologies has resulted actionable real-time data that go beyond simply providing valuable insights. These advancements enable precise control over drilling operations, reducing the likelihood of incidents and improving overall drilling performance (Suranga C. H. Geekiyanage et al., 2020).
The rise of predictive maintenance technologies allows for monitoring equipment conditions and predicting failures before they occur, further minimizing downtime and enhancing productivity. As these automated systems become increasingly sophisticated, they are not only streamlining workflows but also ensuring that critical data is accurately interpreted to support effective decision-making (Suranga C. H. Geekiyanage et al., 2020). Consequently, the shift towards automated rigs represents a significant leap forward in the oil and gas industry, underscoring the importance of embracing digitalization to meet the challenges and demands of modern drilling operations.
Automation in Drilling Operations
Automated drilling rigs are transforming operations in the oil and gas industry by integrating advanced technologies that enhance efficiency and safety. These systems utilize sophisticated algorithms and machine learning to analyze vast amounts of data generated during drilling, allowing for real-time adjustments to operational parameters. This capability not only streamlines workflows but also ensures that interventions are based on accurate and timely data interpretation, which is essential for effective decision-making (Suranga C. H. Geekiyanage et al., 2020).
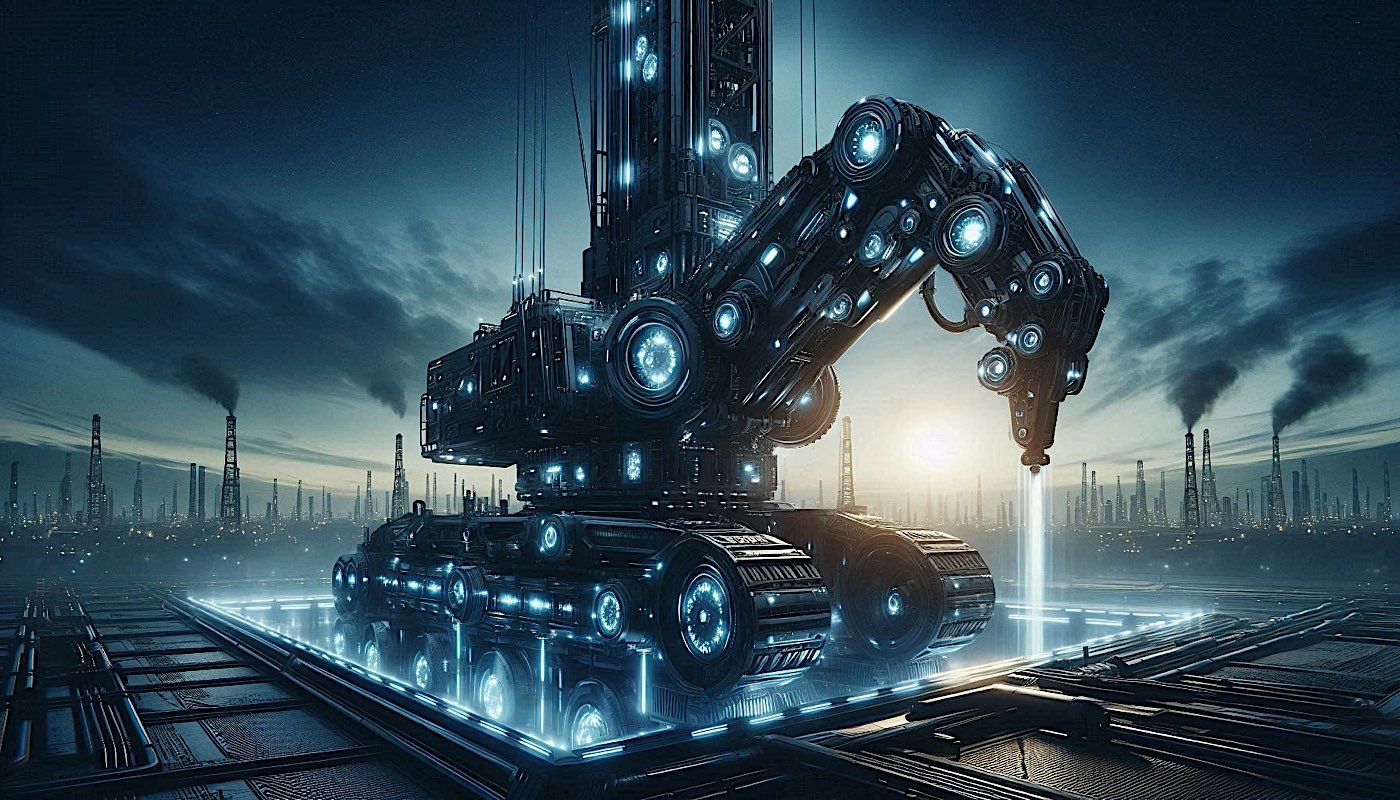
The implementation of predictive maintenance technologies has revolutionized how equipment reliability is managed; by continuously monitoring the condition of drilling equipment, these systems can forecast potential failures before they occur. This proactive approach significantly reduces unplanned downtime, resulting in increased productivity and lower operational costs. Furthermore, automated rigs contribute to improved safety by minimizing human error and providing precise control over drilling operations. By leveraging digitalization, companies can mitigate drilling incidents and optimize processes, thereby enhancing overall performance (Suranga C. H. Geekiyanage et al., 2020).
As the industry continues to adopt automation, it is expected that the operational landscape will evolve, with a greater emphasis on intelligent systems that support seamless integration and data management, ultimately driving the future of drilling operations towards higher efficiency and safety standards.
Real-Time Data Analytics in Drilling
Real-time data analytics plays a pivotal role in enhancing decision-making and operational efficiency in drilling operations. By continuously collecting and analyzing data from various sources, such as drilling equipment, geological sensors, and environmental monitors, operators can gain immediate insights into the drilling process. This constant flow of information enables engineers to make informed decisions based on current conditions rather than relying on outdated data.
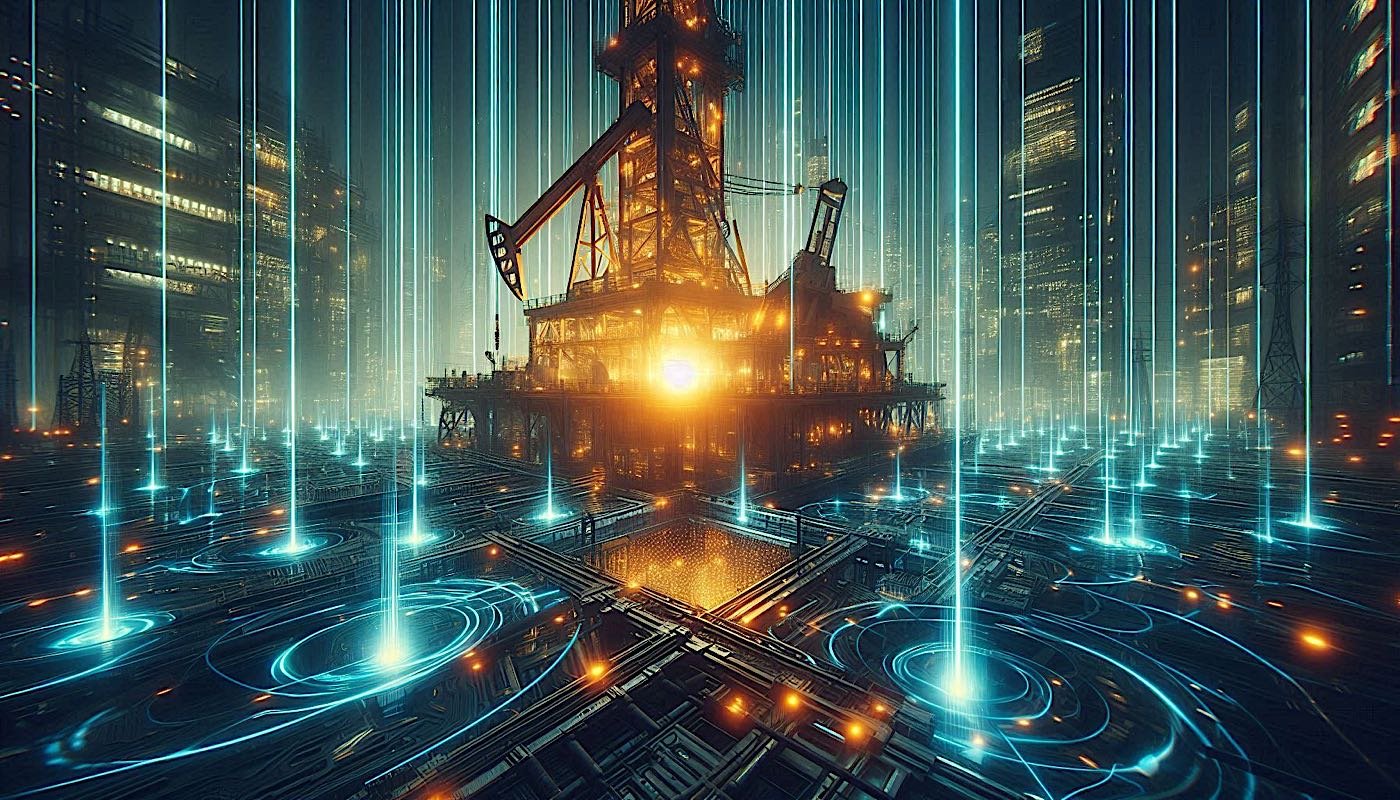
Integrating real-time data allows for proactive monitoring of drilling parameters, such as pressure and temperature, can help in identifying potential issues before they escalate into costly failures (Onyebuchi Uchendu et al., 2024). This immediacy in data assessment fosters adaptive management strategies, where operators can quickly adjust drilling techniques in response to changing geological formations or equipment performance.
The ability to analyze large datasets in real time not only improves the accuracy of predictive models but also enhances operational safety by reducing human error through automation (Suranga C. H. Geekiyanage et al., 2020). Consequently, the integration of real-time analytics is transforming traditional drilling methodologies, leading to increased productivity, reduced downtime, and ultimately, optimized resource extraction. As the industry continues to evolve with advancements in big data technologies and predictive analytics, the potential for even greater efficiencies and safer practices in drilling operations becomes increasingly attainable.
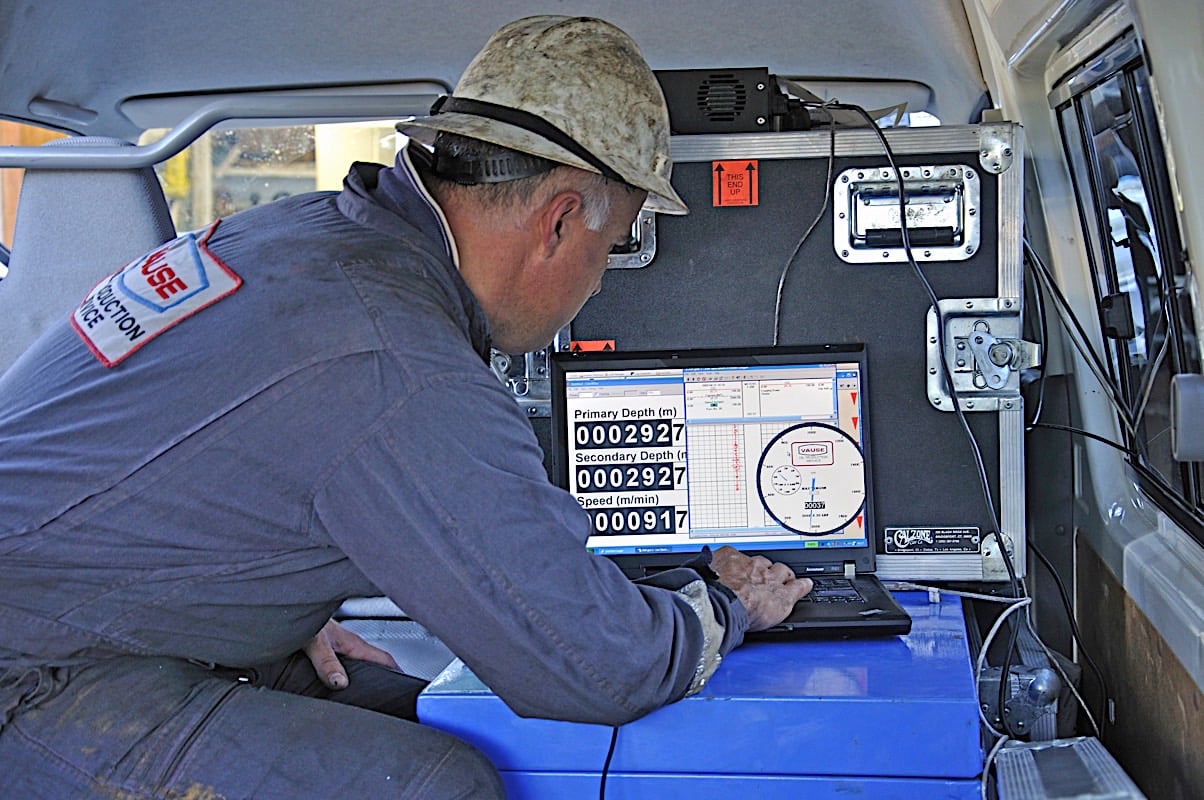
Predictive Maintenance and Equipment Management
They escalate into costly failures (Onyebuchi Uchendu et al., 2024). Additionally, this immediacy in data assessment fosters adaptive management strategies, where operators can quickly adjust drilling techniques in response to changing geological formations or equipment performance. The ability to analyze large datasets in real time not only improves the accuracy of predictive models but also enhances operational safety by reducing human error through automation (Suranga C. H. Geekiyanage et al., 2020).
The integration of real-time analytics is transforming traditional drilling methodologies, leading to increased productivity, reduced downtime, and ultimately, optimized resource extraction. Predictive maintenance strategies leverage real-time data and machine learning algorithms to anticipate when equipment is likely to fail, enabling proactive interventions that prevent unplanned outages. By continuously monitoring equipment conditions, such as temperature and pressure, engineers can set thresholds that trigger alerts for maintenance before issues escalate, thereby ensuring smoother operations.
This approach not only minimizes disruptions but also extends the lifespan of machinery, as timely maintenance can address minor problems before they cause significant damage. Furthermore, the cost savings associated with reduced downtime and maintenance expenses contribute positively to overall profitability. As the oil and gas industry increasingly embraces these advanced technologies, the role of predictive analytics in enhancing equipment reliability and operational efficiency cannot be overstated.
Case Studies of Innovation in the Field
As the oil and gas industry adopts automation and data analytics, several case studies have emerged that highlight the significant benefits of these technologies in drilling operations. For instance, companies are implementing predictive maintenance strategies that utilize real-time data gathered from various sensors to forecast equipment failures.
This proactive approach allows engineers to intervene before issues escalate, thereby reducing unplanned outages and increasing operational efficiency.
Specifically, by closely monitoring critical parameters such as temperature and pressure, organizations can establish alert thresholds that trigger necessary maintenance interventions. In one case study, a drilling operation reported a 20% reduction in downtime due to the implementation of automated monitoring systems, which allowed for timely repairs and minimized disruptions to production schedules.
The integration of advanced machine learning algorithms into drilling processes has enabled more precise data interpretation, leading to enhanced decision-making capabilities. This trend aligns with the broader movement towards digital oilfields, where intelligent systems manage vast amounts of data to optimize drilling performance and safety (Suranga C. H. Geekiyanage et al., 2020).
By leveraging these innovations, drilling operations not only enhance equipment reliability but also achieve substantial cost savings, reinforcing the importance of automation and data analytics in driving the industry forward.
References
•Suranga C. H. Geekiyanage, Andrzej T. Tunkiel, & D. Sui. (2020). Drilling data quality improvement and information extraction with case studies. In Journal of Petroleum Exploration and Production (Vol. 11, pp. 819–837). https://doi.org/10.1007/s13202-020-01024-x
•Onyebuchi Uchendu, Kingsley Onyedikachi Omomo, & Andrew Emuobosa Esiri. (2024). The concept of big data and predictive analytics in reservoir engineering: The future of dynamic reservoir models. In Computer Science & IT Research Journal. https://doi.org/10.51594/csitrj.v5i11.1708
•I. Sorokina, V. Dvoyrin, N. Tolstik, & E. Sorokin. (2014). Mid-IR Ultrashort Pulsed Fiber-Based Lasers. In IEEE Journal of Selected Topics in Quantum Electronics (Vol. 20, pp. 99–110). https://doi.org/10.1109/JSTQE.2014.2310655
•Saeed Hasan Al Zaabi, & Ruzaidi Zamri. (2022). Managing Security Threats through Touchless Security Technologies: An Overview of the Integration of Facial Recognition Technology in the UAE Oil and Gas Industry. In Sustainability. https://doi.org/10.3390/su142214915
•Behrouz Liravinia, Mahmoud Modiri, & Kiamars Fathi Hafshjani. (2023). Identification and Evaluation of the Design Risks in Iran’s Oil, Gas and Petrochemical Industry. In Journal of information and organizational sciences. https://doi.org/10.31341/jios.47.1.2
•Muhammad Naeem, A. Khalil, Zeeshan Tariq, & M. Mahmoud. (2022). A Review of Advanced Molecular Engineering Approaches to Enhance the Thermostability of Enzyme Breakers: From Prospective of Upstream Oil and Gas Industry. In International Journal of Molecular Sciences (Vol. 23). https://doi.org/10.3390/ijms23031597
•Xiaoyong Li, Lihui Zheng, Yuanbo Chen, Xiaowei Huang, Xiaopeng Zhai, Panfeng Wei, Xiujuan Tao, & Shuaishuai Nie. (2023). Fuzzy-Ball Fluids Enhance the Production of Oil and Gas Wells: A Historical Review. In Energies. https://doi.org/10.3390/en16186647
• E. Epelle, & Dimitrios I. Gerogiorgis. (2019). A review of technological advances and open challenges for oil and gas drilling systems engineering. In AIChE Journal. https://doi.org/10.1002/aic.16842
•Batirova Uldaykhan Sarsenbaevna, Tajetdinova Gulnora Abatbay qizi, & Karjaubayev Marat Ospanovich. (2024). THE PROCESS OF DRILLING OIL AND GAS WELLS. In The American Journal of Applied Sciences. https://doi.org/10.37547/tajas/volume06issue06-08
•E. Leonov, & V. I. Isaev. (2009). Applied Hydro-Aeromechanics in Oil and Gas Drilling. https://doi.org/10.1002/9780470542392
•A. Mady, O. Mahmoud, & A. Dahab. (2020). Nanoparticle-based drilling fluids as promising solutions to enhance drilling performance in Egyptian oil and gas fields (Vol. 1, pp. 24–38). https://doi.org/10.21608/ijisd.2020.73471
•Yu Fu, & Fuwei Li. (2023). Research and Evaluation of Efficient Drilling Speedup Supporting Technologies and Cementing Processes for Ultra-deep Wells. In Frontiers in Science and Engineering. https://doi.org/10.54691/fse.v3i8.5529