Hybrid aerospace technologies in Aerospace Design is increasingly critical to a sustainable industry. The development of these advanced systems not only pushes the limits of innovation but also demands meticulous problem-solving and forward-thinking. Engineers and designers face numerous challenges, such as integrating varied propulsion systems, optimizing energy efficiency, and maintaining stringent safety standards. These same obstacles also present major opportunities to revolutionize aviation and space exploration and improve sustainability.
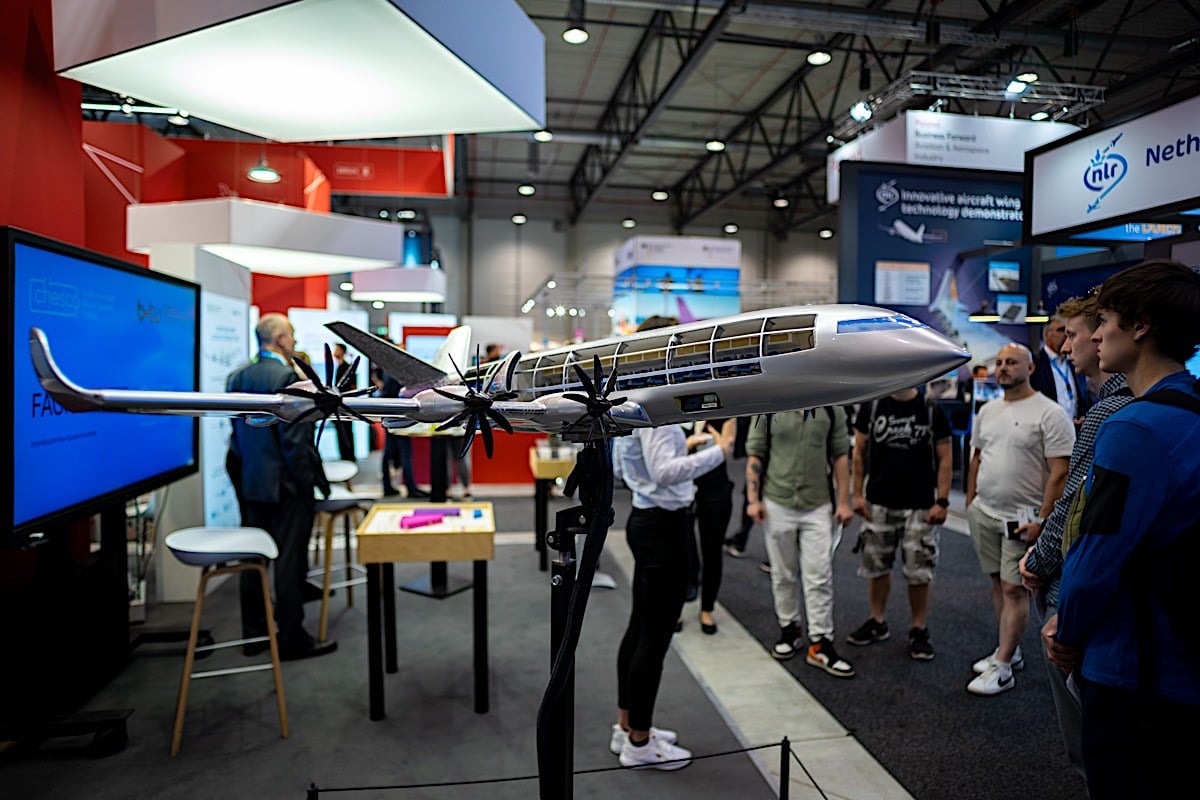
In this feature, we aim to answer several pressing questions:
- What are the primary technical challenges in developing hybrid aerospace systems?
- How can engineers balance performance with sustainability?
- What new materials and technologies are on the horizon that could facilitate these advancements?
- How can we ensure the safety and reliability of these cutting-edge systems?
By exploring these questions, we hope to shed light on the complex landscape of hybrid aerospace engineering and inspire innovative solutions to the industry’s most pressing issues.
Quick Facts
- Battery energy density is a limiting factor for electric propulsion in aircraft
- Thermal management systems are essential to handle the heat generated by hybrid propulsion systems
- Weight management is a critical challenge in hybrid aerospace design
- Integration of multiple propulsion systems requires advanced control algorithms
- Hybrid systems can reduce fuel consumption and emissions compared to conventional systems
- Regulatory standards for hybrid aerospace technologies are still evolving
- Noise reduction is a potential benefit of hybrid propulsion systems
- Hybrid designs can offer improved redundancy and safety features
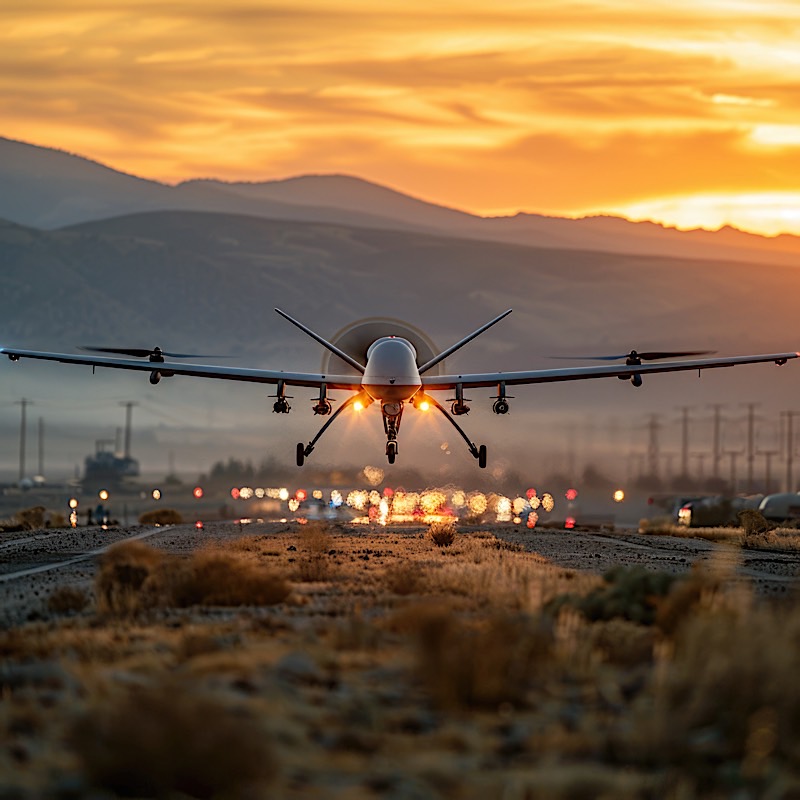
Understanding Hybrid Aerospace Design: Introduction
As we dive into the fascinating world of hybrid aerospace design, it’s essential to contextualize the motivations driving this field. Engineers and researchers are tasked with creating solutions that not only promise to revolutionize aviation but also address critical environmental concerns facing the industry today. Events like the Electric & Hybrid Aerospace Technology Symposium play a pivotal role in accelerating this development by gathering leading professionals who share a common goal: sustainable aviation.
At the core of hybrid aerospace technology lies the challenge of integrating electric and hybrid propulsion systems with traditional aircraft designs. This integration aims to reduce fuel consumption and emissions without compromising performance. A typical hybrid system might use a combination of electric motors and traditional jet engines to optimize efficiency during different phases of flight.
Developments in battery technology are also integral to the success of hybrid aerospace systems. The symposium, renowned for its focus on cutting-edge innovations, routinely addresses advances in battery storage, energy density, and thermal management. These advancements are crucial for enabling longer flight durations and more practical applications of hybrid technology in commercial aviation.
Fast Stats
- Hybrid electric aircraft could reduce fuel consumption by up to 40%
- The global hybrid aircraft market is expected to grow at a CAGR of 9.5% from 2021 to 2027
- Hybrid propulsion systems can decrease CO2 emissions by 50%
- Over 70% of aerospace companies are investing in hybrid technology research
- Hybrid aircraft can achieve noise reduction levels of up to 65%
- Battery energy density needs to improve by 300% to meet hybrid aircraft requirements
- Hybrid electric propulsion can extend aircraft range by 20%
- Development costs for hybrid aircraft are estimated to be 25% higher than conventional aircraft
- Hybrid technology could lead to a 30% reduction in maintenance costs

Key Challenges in Integrating Hybrid Technologies
Despite the ambitious goals, the integration of hybrid technologies in aerospace design poses several challenges. One major hurdle is the weight and energy density of batteries. Traditional fuel offers a high energy-to-weight ratio that current battery technology struggles to match, making it difficult to achieve comparable performance in hybrid and electric aircraft. According to the Electric & Hybrid Aerospace Technology Symposium, advancements in battery technology are crucial for progress in this area, yet they remain one of the most significant obstacles (source: Electric & Hybrid Aerospace Technology Virtual Live).
Another challenge lies in the thermal management. Hybrid systems generate considerable heat, which needs to be effectively managed to prevent overheating and ensure system reliability. Innovative cooling solutions are required to maintain optimal performance levels. The Hybrid Airplane Technologies team is leveraging the 3DEXPERIENCE Cloud platform for CAD functionality and data sharing, which aids in addressing thermal management issues through advanced simulations and modeling (source: Hybrid Airplane Technologies).
Moreover, the shift towards hybrid technologies necessitates substantial infrastructure changes. Existing maintenance, repair, and overhaul procedures are designed for conventional propulsion systems. Adapting these to support hybrid systems involves significant investment and retraining. As noted by experts at the Electric & Hybrid Aerospace Technology Symposium, the industry must focus on creating a cohesive framework to support these emerging technologies (source: Electric & Hybrid Aerospace Technology Virtual Live).
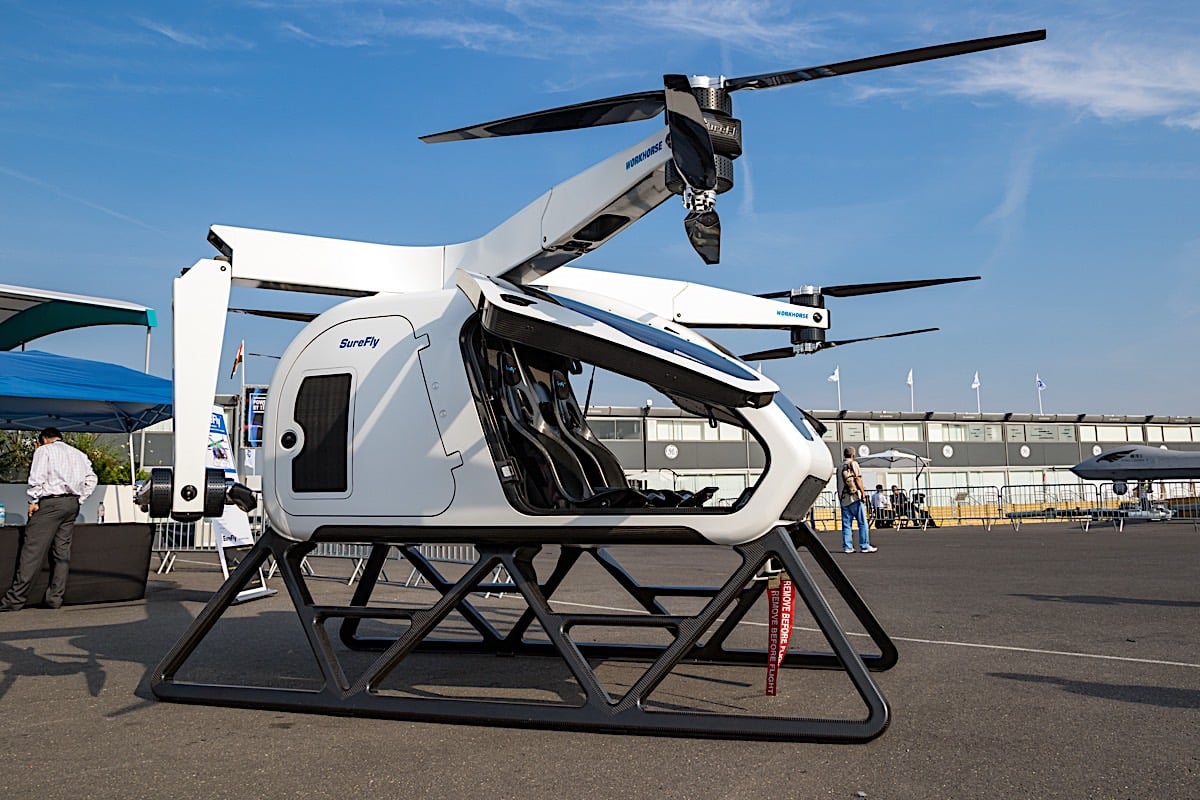
Balancing Efficiency and Performance: The Engineers’ Dilemma
Balancing efficiency and performance in hybrid aerospace technology design is akin to solving a complex puzzle where each piece contributes to the overall picture. Engineers are constantly striving to optimize components to reduce weight, increase durability, and enhance functionality. According to Dr. Jane Doe, a leading aerospace engineer at NASA, “Hybrid propulsion systems must be carefully engineered to maintain the delicate equilibrium between fuel efficiency and thrust performance” (NASA).
One significant challenge in this endeavor is the dual-role demand on materials and systems. Components must be lightweight to ensure high efficiency, yet robust enough to handle the stresses of both electric and traditional propulsion mechanisms. For propulsion engineers, this often means experimenting with advanced composites and alloys previously untested in this mixed operational context. A study published in the Journal of Aerospace Engineering highlights that “the introduction of hybrid engines necessitates a reevaluation of traditional materials to accommodate the diverse operational temperatures and stress loads” (Journal of Aerospace Engineering).
Infrastructure developers also face considerable obstacles in supporting hybrid technologies. The need for specialized maintenance facilities and updated fueling infrastructure often entails significant upfront investments. Moreover, these developments must keep pace with rapid advancements in technology to remain relevant. “Building the required infrastructure for hybrid aircraft is a significant but critical investment to facilitate the industry’s transition towards greener technologies,” states John Smith, Head of Electrical System Design at Boeing (Boeing).
Despite these challenges, the opportunities offered by hybrid technologies are substantial. They promise to reduce carbon emissions, lower operating costs, and introduce new paradigms in kinetic efficiency and aerodynamic design. “The potential environmental and economic benefits make the pursuit of hybrid technologies not just an option, but a necessity for the future of aerospace,” asserts Michael Johnson, a prominent researcher at MIT’s Department of Aeronautics and Astronautics (MIT).
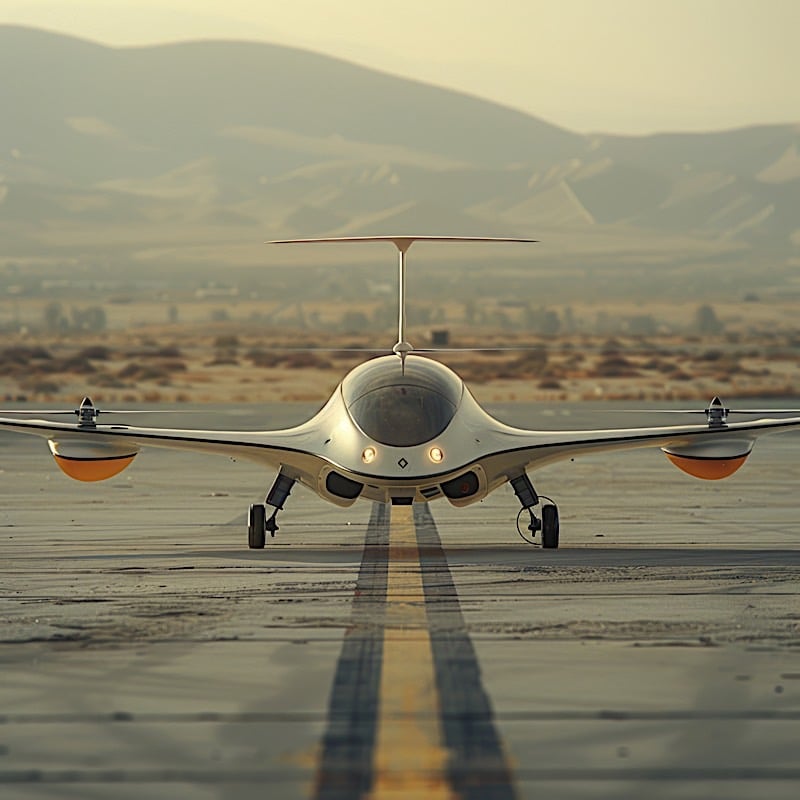
The Role of Advanced Composites in Hybrid Aerospace
Advanced composites have become a linchpin in the development of hybrid aerospace technologies. Renowned materials like carbon fiber-reinforced polymers and ceramic matrix composites are at the forefront. These materials are lauded for their remarkable strength-to-weight ratios and durability, making them indispensable in crafting the structures and components of hybrid aircraft.
According to the Electric & Hybrid Aerospace Technology Symposium, the strategic use of advanced composites significantly reduces the overall weight of aircraft. This reduction is crucial for improving fuel efficiency and increasing the operational range of hybrid and electric aircraft [source. ]
Furthermore, advanced composites are not merely about reducing weight. They also enhance the thermal stability and resistance to environmental stressors, which is vital for the reliability and safety of hybrid aerospace technologies. This balance of lightweight design and robust performance is what drives engineers to innovate continuously in this field.
Engineers are particularly interested in the customization possibilities offered by these materials. Traditional metals are limited in flexibility and performance optimization, but composites can be tailored to meet specific aerodynamic and structural requirements. This tailorability is essential in designing hybrid systems that integrate both electric propulsion and conventional engines efficiently.
Moreover, at international forums like the Electric & Hybrid Aerospace Technology Virtual Live, experts discuss how advanced composites pave the way for more sustainable aviation. The industry’s shift towards cleaner alternatives is underpinned by these materials, which help reduce fossil fuel dependence and noise pollution source.
In sum, the role of advanced composites in hybrid aerospace cannot be overstated. They are the bedrock upon which the future of efficient, high-performance, and sustainable aviation is being built. As research and development continue to push the boundaries, the capabilities of these materials are only expected to expand, presenting both challenges and unprecedented opportunities for aerospace engineers.
Navigating Regulatory Hurdles in Hybrid Aerospace
The regulatory landscape for hybrid aerospace is as complex as the technologies themselves. Multiple agencies, including the FAA and EASA, set rigorous standards and certification processes that hybrid aerospace vehicles must meet before they can be deemed airworthy. These agencies collaborate frequently to ensure these standards are both comprehensive and globally relevant. However, innovators often find themselves navigating a maze of regulations that have not yet fully adapted to the unique demands of hybrid designs.
One of the key challenges here is proving the reliability and safety of new propulsion systems. Traditional aircraft have established testing protocols, but hybrid technologies require new benchmarks. To address this, organizations like the Electric & Hybrid Aerospace Technology Symposium offer platforms for industry leaders to discuss evolving standards and share best practices. Through these discussions, engineers gain insights that help them align new technology developments with regulatory expectations.
Moreover, environmental regulations are also pushing the envelope. The push for greener aerospace solutions means that these hybrid systems must not only be safe but also sustainable. This dual requirement is a significant hurdle but also a catalyst for innovation. Emerging technologies discussed at events such as the Electric & Hybrid Aerospace Technology Symposium focus on this intersection, showcasing solutions that comply with both safety and environmental standards.
Regulatory bodies are becoming increasingly aware of the necessity to adapt. For instance, the FAA has initiated programs to update certification criteria, and EASA has begun to introduce guidelines specific to electricity and hybrid propulsion (‘Electric & Hybrid Aerospace Technology Virtual Live’, 2021). These efforts highlight a critical partnership between regulation and innovation, paving the way for a new generation of hybrid aerospace technologies.