The heart of oil and gas operations lies in the extraction, refinement, and transportation of these precious resources. It’s a complex, high-risk industry riddled with a range of safety and efficiency issues. The engineers and designers tasked with easing these burdens are continually driven to find innovative solutions. One such solution they’re exploring today is robotics. Robots, designed with advanced technologies, have ventured a promising way forward, promising enhanced safety and efficiency in oil and gas operations. But before we delve into the solutions, let’s lay the groundwork by identifying the existing problems.
The Problem Spectrum: Safety and Efficiency Concerns
The oil and gas industry has continually grappled with numerous health and safety issues, from the hazardous environments employees work in, to the risky nature of the tasks. In addition to these, the fluctuating demand for these resources and the crippling costs of extraction and transportation have also been plaguing the industry, hindering efficiency.
Fast Facts:
- The oil and gas sector has one of the highest rates of severe injury, according to the U.S. Bureau of Labor Statistics.
- Oil and gas drilling activities are prone to cost overruns, with about 64% of mega-projects facing high unexpected costs, as per the ExxonMobil report.
- Robotic applications may reduce human error, thus potentially saving lives and reducing the risk of costly accidents (PwC report).
Robotics Solutions to Safety and Efficiency Problems
Robotic Solutions for Safety To mitigate safety risks in oil and gas operations, robotics offer a reliable way to conduct dangerous tasks. This effectively removes human workers from high-risk environments. For example, the use of ground robots for inspections in harsh or confined spaces is a huge leap towards ensuring worker safety (source: Robotic Business Review).
Efficiency Problems
It’s fair to say that the oil and gas industry is in constant need of ways to ensure robust operational processes and efficiency. It’s here that the power of robotics can make a transformative change.
Let’s consider some serious problems first.
While it’s critical to maintain a steady flow of energy to fuel our daily operations, several issues exist that could disrupt this process. Concerning the oil and gas industry, these issues often present themselves in the form of safety and efficiency challenges.
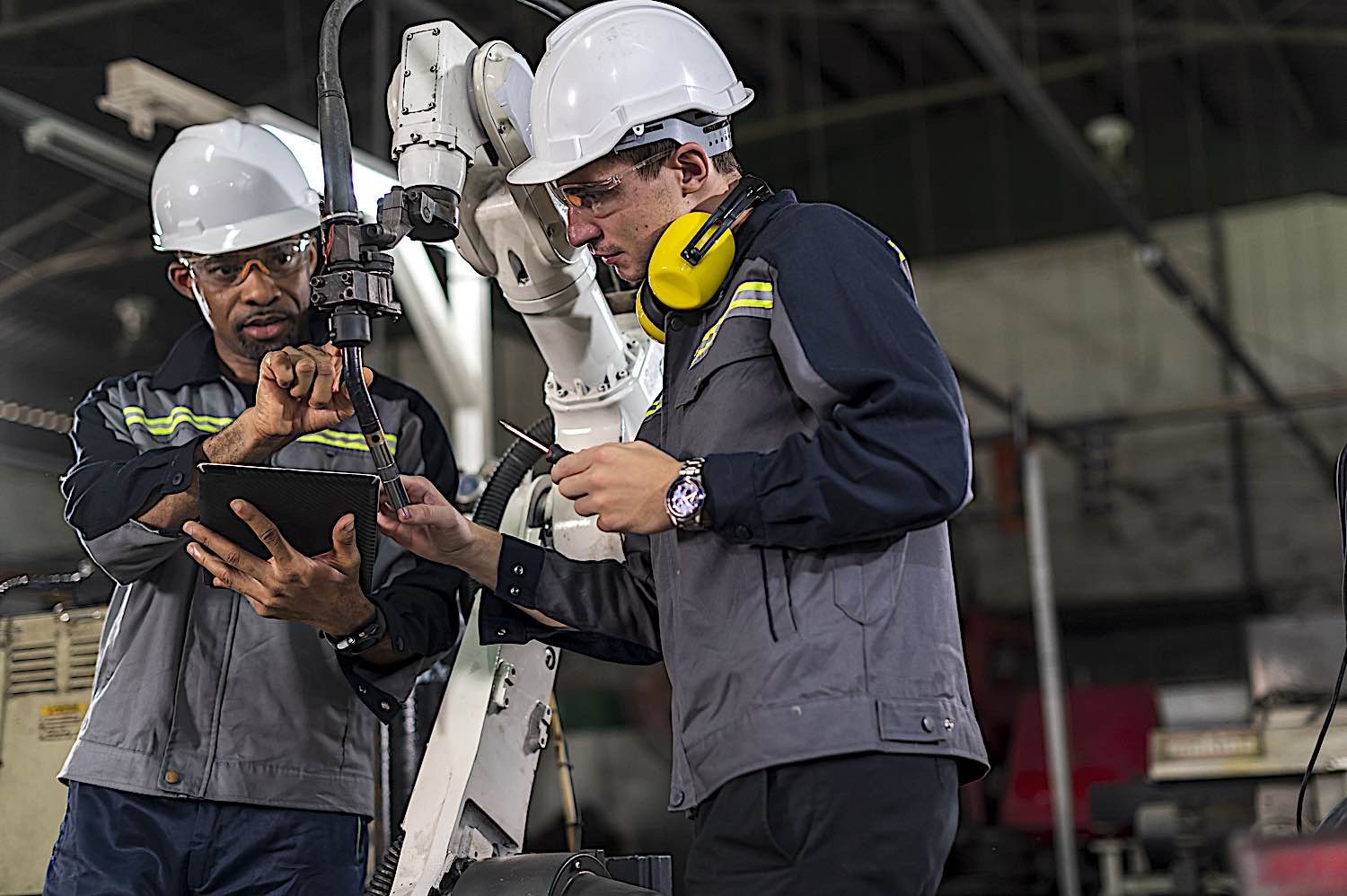
Safety Problems
Despite the precautions and protocols in place, accidents might still happen, given operations are often undertaken in hazardous conditions. Prolonged exposure to heat, high pressure, or toxic chemicals can lead to health problems or, worse, life-threatening situations for workers.
Aside from human safety, risk factors such as unexpected equipment failure can also lead to significant economic loss. Imagine having to stop production simply because of a faulty valve or a broken pipe—it doesn’t sound like a walk in the park, right?
Let’s shine the spotlight on the other side—efficiency. With fields and reserves often located in remote or inaccessible regions, logistics and operations can turn into a herculean task. Furthermore, wielding manual control over vast geographical lines and complex systems can push up the likelihood of inefficiencies and operational errors.
Robotic Solutions for Efficiency
So, is there a way to tackle these obstacles head-on, ensuring both safety and efficiency, and alleviating these burdens?
The use of robots in the oil and gas industry presents an innovative solution to these pressing problems. Deploying robotics can introduce safer and more efficient modes of operations. Robots, unlike their human counterparts, can work under extreme conditions without fatigue. This not only shields workers from harmful environments but also precludes the need for potential costly shutdowns.
Focusing on efficiency, the application of robotics offers the capability of performing precise and rapid tasks, inevitably saving time and internal resources. Robots can reach places difficult for humans, perform tasks beyond human capabilities, and work round-the-clock without the need for breaks. This, combined with their capability to minimize errors, transforms them into a potent tool for enhancing operation efficiency.
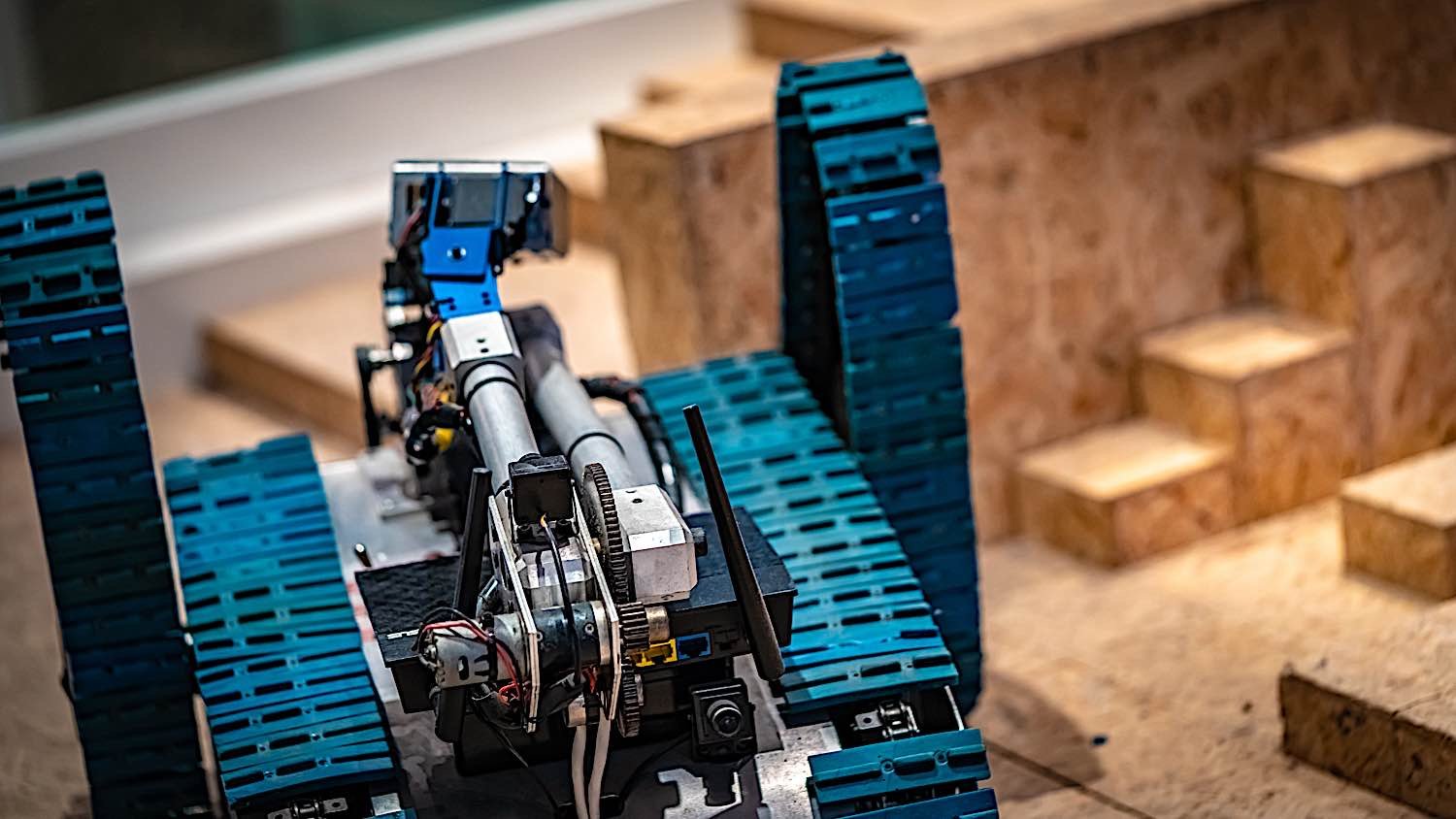
Tackling Hazardous Environments: How Robots Are Keeping Workers Safe
When it comes to safety, robotics are revolutionizing the field for oil and gas operations. Here are three notable examples where robotics have made a significant impact:
1. Robotic Snakes – In partnership with the Norwegian research group SINTEF, oil and gas company Eelume developed a robotic snake designed to live permanently under water to perform maintenance duties, reducing the use of large and costly underwater vehicles. By doing this, the robotic snake mitigates the human risk in such hazardous environments[1].
2. Inspection Robots – Many oil and gas firms deploy inspection robots, like the kind used by Diakont, to assess the quality and safety of tanks, pipelines, and other infrastructure. The robots use high-resolution cameras and laser scanners to detect cracks and corrosions that could create health and safety problems if left unchecked[2].
3. Drilling Robots – Companies like Shell and Ensign Energy Services are using drilling robots to do the physically demanding job of connecting drill pipes. By taking over this manual task, drilling robots protect workers from potential harm and the physically-taxing labor[3].
These are just a handful of the ways in which robotics are keeping oil and gas industry workers safe. These technological advances have already made a significant difference and as they continue to evolve, their influence promises to be truly transformative for the sector.
Optimizing Inspections: Utilizing Robotics for Enhanced Safety and Accuracy
You’re likely already aware of the numerous hazards and risks that the oil and gas industry has to deal with daily. Rigorously inspecting the infrastructure associated with extraction and distribution plays a crucial part in mitigating these hazards. Yet these inspections can be time-consuming and often carry considerable risks for the human inspectors.
This is where robotics technology comes to the rescue. Robots are being increasingly used as potent tools in performing inspections in challenging or dangerous environments without placing human lives at risk. The InnovOil report (2019) highlighted how robots, being immune to physical harm, can take on tasks dangerous and unsafe for humans, such as traversing high-risk areas or withstanding exposure to harmful gases or extreme temperatures[1].
But the benefits of using robots aren’t limited to safety alone. In fact, adopting robotics technology can dramatically improve the accuracy of inspections, too. Ever heard of underwater drones or remotely operated vehicles (ROVs)? These are being used for underwater inspections of subsea pipelines, off-shore platforms, and the hulls of tankers[2]. According to an article published on ENR, these robotic marvels can capture HD video and 3D-model data with accuracies previously unthinkable. Casually said, these robots don’t just do inspections; they redefine the very nature of inspections in the industry[2].
Efficiency? Check. Safety? Check. Accuracy? Check. You can see how using robotic technology for inspections opens up a world of possibilities for the oil and gas industry.
Mitigating Human Error: How Robots Are Minimizing Risks in Oil and Gas Operations
Undoubtedly, human error remains a significant concern in oil and gas operations. Like in any other industry, the activities of humans are bound by limitations of fatigue, attention, and unforeseen circumstances which can sometimes lead to fatal mistakes that not only jeopardize safety but have a significant toll on productivity. Robots: Taming the Unpredictable
However, with robotics, the industry has started to witness a remarkable change. From simple repetitive tasks to complex maneuverability, robots are designed to perform functions with an extreme level of precision. They are neither prone to fatigue nor do they have lapses in attention, minimizing human-like errors that can derail safety and efficiency in oil and gas operations. [source] Automated Inspections, Fewer Mistakes
One area where robots excel is in the inspection of oil and gas facilities. Robots equipped with advanced sensors and imaging devices ensure accurate assessment of the structural integrity of the facility, pipe thickness, and corrosion levels. This automation removes the likelihood of overlooking a potential risk area due to human error, thereby potentially preventing catastrophes. Data Analysis: Unmasking the Hidden Risks
Robotics isn’t just about physical automation; it’s also about data analysis. Robots can amass and analyze large volumes of data swiftly and more accurately than humans. This ability can unveil patterns or signs that indicate potential equipment failure or other operational anomalies. As a result, early detection and resolution become possible, reducing the margin for error significantly. [source] Bridging the Training Gap
In addition, robots can bridge the often overlooked training gap. In several situations, human errors can be attributed to a lack of training or a misunderstanding of system functions. The implementation of robots can reduce this variable drastically, as they come programmed to follow selected protocols and standards impeccably.
Improving Maintenance Practices: The Benefits of Robotic Technology
Advancements in robotic technology have been instrumental in enhancing maintenance practices in the oil and gas sector. Traditionally, regular machinery inspections and overhauls were critical for maintaining operational efficiency as well as mitigating safety risks. However, these maintenance tasks often posed numerous challenges, including hazardous work conditions, labor-intensive tasks, and significant downtimes.
Today, robotics has revolutionized how maintenance tasks are carried out in this industry. For instance, companies are using automated robots to perform regular inspections and maintenance in hazardous sites such as off-shore oil rigs and drilling platforms. One excellent example is BP’s deployment of robotic drones for carrying out routine inspections on its Thunder Horse platform in the Gulf of Mexico. This implementation of aerial robots has significantly reduced human exposure to hazardous conditions, increased inspection frequency, and improved the quality of maintenance data collected, according to BP magazine.
Furthermore, robotic technology in maintenance practices has proven to be a game-changer in minimizing operational downtimes. In a report by the CIOReview, they illustrated how robotic crawlers can perform internal inspections of pipes while they are still in operation. This means that companies can now conduct maintenance checks without having to shut down their operations, thereby significantly reducing operational downtimes and increasing productivity.
Finally, with advancements in machine learning and artificial intelligence, maintenance robots are now equipped with predictive maintenance capabilities. By analyzing the collected data, these robots can identify potential issues before they occur and recommend preventive measures to prevent system failure or breakdowns. A key player in this aspect is Baker Hughes, which offers a predictive maintenance product that uses machine learning algorithms to predict machine failures days or weeks in advance, enhancing the overall lifespan of machinery and significantly reducing maintenance costs.
These examples underscore the significant benefits conferred by the advent of robotics in the maintenance practices of the oil and gas sector, driving safety improvements, operational efficiency, and cost savings.
Increasing Productivity: Exploring the Efficiency Gains with Robotics
You probably know well that the profitability of oil and gas operations largely hinges on productivity. But boosting productivity isn’t always easy, is it? Especially when you’re up against factors like harsh conditions, equipment breakdowns, and the sheer scale of operations. Not to mention the environmental concerns and regulatory requirements that can tie up resources.
But what if you could tackle those challenges head-on? Enter robotics. Embracing robotics may enable you to streamline operations, boost productivity, and cut down on unnecessary downtime. In fact, a study by McKinsey and Company points out that robotic automation can increase productivity by up to 20 percent for numerous processes in the oil and gas sector. [source]
How, you ask? Robots can operate round the clock without experiencing fatigue, making them ideal for tasks requiring continuous operations. Whether it’s drilling, extracting oil, or inspecting pipelines, robots can maintain a consistent level of performance that invariably results in an uptick in productivity.
It is not just about the physical tasks, either. Robots equipped with artificial intelligence can handle complex data analysis, predictive modeling, and decision-making tasks, freeing up your human teams to focus on tasks requiring nuanced judgement and creativity.
In other words, with robotics at your disposal, what seemed like insurmountable productivity challenges may just turn into golden opportunities for enhancement and growth. Indeed, the oil and gas industry’s future might just be robotic.