Even though government regulation has forced carmakers to build more and more fuel-efficient, “greener” cars in the last couple of decades, the manufacturing process itself is far from environmentally friendly. The discussion and innovation have focused on how we fuel cars, while the larger issue of the manufacturing process, with all of the input, materials and energy that go into such a complex product as a car, has largely been ignored. A San Francisco company called Divergent Microfactories (DM) says that the solution lies in building “dematerialized” cars, and distributing the technology so that small groups around the world can build their own cars with it.
Dematerialized cars are greener because they use fewer resources and produce less pollution during their manufacture. They are also much lighter—up to 90 per cent lighter than traditional vehicles, while still being strong and durable. And they are safer, so the company claims, though this is something not yet put to the test. “At Divergent Microfactories,” said CEO Kevin Czinger, “we’ve found a way to make automobiles that holds the promise of radically reducing the resource use and pollution generated by manufacturing. It also holds the promise of making large-scale car manufacturing affordable for small teams of innovators.”
The headline benefit of the DM-produced supercar called Blade (photo above courtesy of DM), just unveiled to the public, is its 3D printing. The car’s chassis incorporates 3D printed “nodes” joined together by off-the-shelf carbon fibre tubing. Nodes are the key building blocks in the process and are made of a metal alloy. With this approach, DM says, they can build a very strong and very light chassis, while saving energy and generating three times less pollution. The company claims it can assemble a complete “industrial strength” chassis in a matter of minutes. This could be done even faster using robotics.
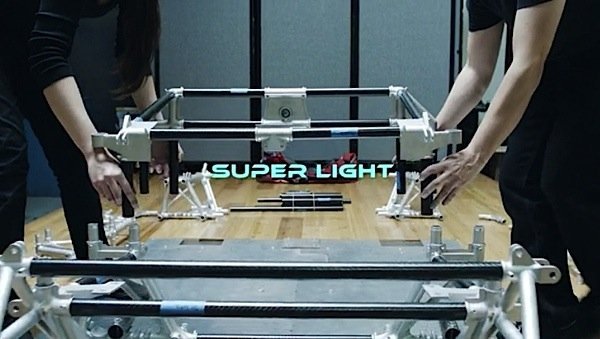
As for the body of the car, the prototype Blade is made of composite, but DM says the body is not structural and could therefore be made of anything, “even spandex.” Blade is powered by a 700 HP 4-cylinder turbocharged internal combustion engine fueled by compressed natural gas or gasoline.
What is potentially disruptive about this is not the car itself. Rather, DM says it is producing the world’s first 3D printed auto manufacturing platform and thereby democratizing the auto industry. Czinger is unapologetic, saying that they are starting a revolution. His aim is not to mass produce cars, but rather to give small teams or “microfactories” around the world the tools to produce their own cars. The platform can be readily adapted to local needs and conditions, from two-seat sports cars to pickup trucks.
The microfactories, which could assemble cars from nodes manufactured at a centralized facility, could produce up to 10,000 cars a year. This would take production of cars out of the control of the major carmakers and make it feasible for every community to have its own car maker. DM estimates that a microfactory could be set up for around $5 million, a fraction of the hundreds of millions of dollars that go into traditional car assembly plants. To set up a fully fitted factory with its own in-house 3D printing capabilities would cost under $20 million.