The missing “technology” in the dream of hypersonic air travel is a light-weight but heat-resistant material that can tolerate the superheating of travelling more than five times the speed of sound (Mach 6 or more). Mach 5 would equate to 3,800 mph or 6,125 km/h. At those speeds, nose tips, wings, turbine blades heat up and degrade due to ablation caused by extreme heat. I the same way ceramics are often used on spacecraft meant for re-entry, hypersonic aircraft must have similar protection — but for longer-term exposure. Current materials degrade — or even evaporate.
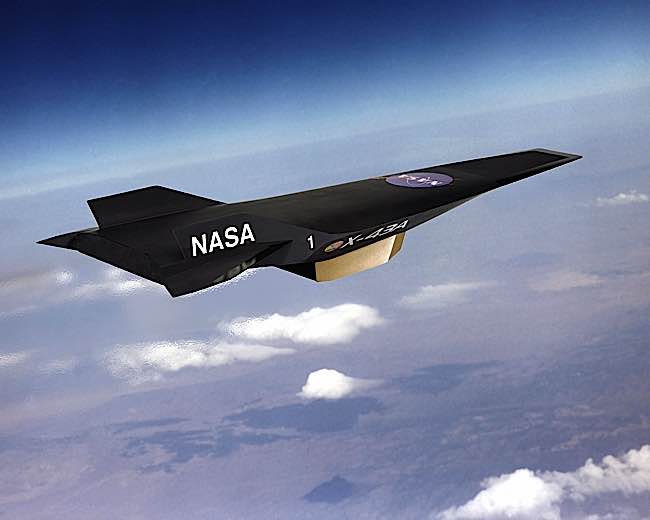
Nasa, have been testing engines and flights — particularly the “X” planes — and others such as Lockheed Martin have concepts and proof of concepts under way. Enter the UHTC teams from the University of Manchester and the Central Souther University of China. UHTC just stands for “ultra-high-temperature ceramics.”
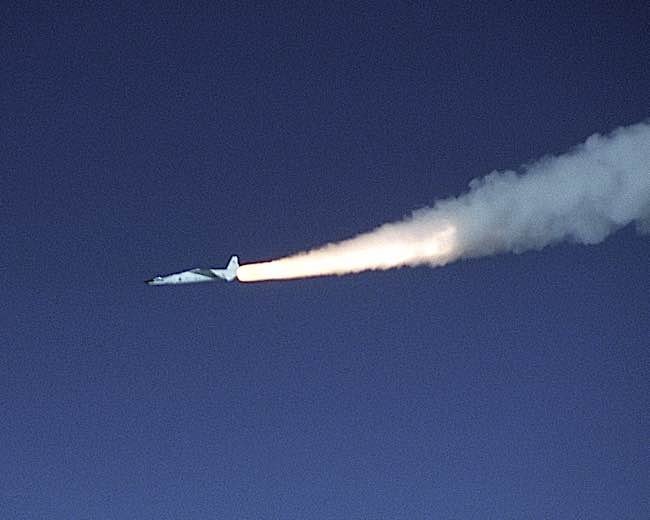
Ceramic Carbide Coating
Coating the exterior with ceramic carbide may be the solution to flying at hypersonic speeds without subsequent heat degradation. According to the University teams, ceramic carbide is 12 times more durable and resilient as compared to current common-use UHTCs such as zirconium carbide (ZrC) or titanium carbide (TiC).
See this chart of various UHTCs and their temperature thresholds:

The new ceramic is made using a method called Reactive Melt Infiltration (RMI), which imposes a mix of elements (Titanium, zirconium and so on) into a composite carbon matrix. The RMI method makes the ceramics far more resistant to degradation caused by heat at hypersonic velocities. Central South University in China made the new ceramic, evaluated at Manchester University.
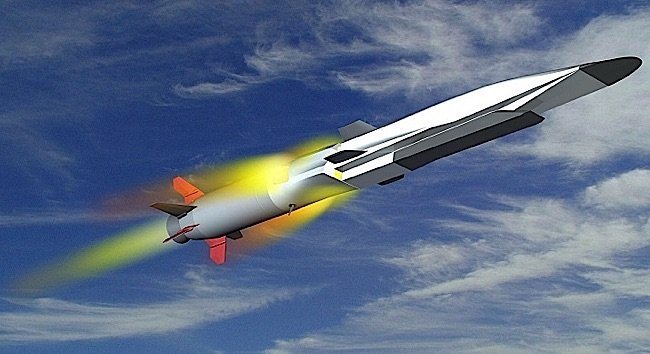
Professor Ping Xia of Materials Science at Manchester University explained: “It has been shown that introducing such ceramics into carbon fiber-reinforced carbon matrix composites may be an effective way of improving thermal-shock resistance.”
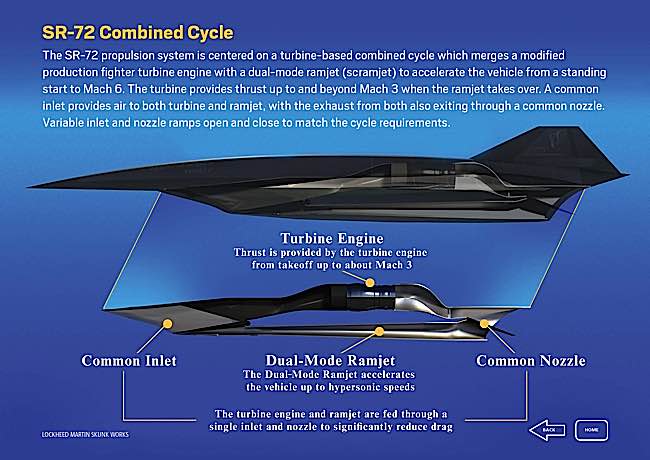