Nowhere is Maintenance, Repair and Overhaul (MRO) more essential than in space — where temperatures and conditions are extreme. SpaceX Commercial Resupply Services Mission-16 is typical of this routine — yet highly complex — operation, with a Robotic Refuelling Mission. Mission 3 in this series will test new methods for transferring and storing cryogenic fluids, such as methane, into space. The lowest cost components, such as seals, retaining rings, plugs and slides can be mission-critical. [See video covering this mission below.]
This mission, focusing on robotic refuelling, is critical to the future of space exploration. It will test refuelling satellites in space — extending their lifespans, to prevent dangerous de-orbiting, among other benefits.

It will also serve as the precursor to refuelling for deep space exploration. Like the famous Canadarm, which facilitated payload handling since 1981 — and today, on board the International Space Station — this new technology will be vital to maintenance. Even the smallest component must endure extreme conditions.

Why is MRO of satellites crucial?
There are 4,857 satellites currently orbiting the Earth — up in 2018 by 4.79 percent since 2017.[1] The simplest components in these important orbiting platforms must endure, in many cases, decades in space. Not only do they face extreme temperatures, radiation, they also may need servicing after an impact with debris in space or micrometeorites.
These satellites are vital to communications, GPS, national security, weather reporting and other essential functions. Maintaining and refuelling have the potential to extend their useful lives and avoid some of the hazards of de-orbiting satellites.
Watch the mission briefing video:
NASA explains, in a bulletin:
“When satellites run out of fuel, they are no longer able to maintain their orbit or stay pointed in the right direction. When they run out of coolant, optical instruments stop functioning correctly. The shell left behind may experience orbital decay or become orbital debris, and a new satellite may need to be launched to take its place, adding a costly expense. When fuel runs low unexpectedly, a satellite’s shutdown may also cause a loss of data and science.RRM3’s methods of storing and transferring cryogenic fluid could give the aerospace industry a practical way to extend the life of satellites and enable long-duration exploration missions. A proven refuelling process could ensure continuity for current satellite infrastructure and greatly expand mission capabilities for satellites travelling beyond low-Earth orbit.” [2]

NASA goes on to explain that refuelling is not simple: “Several fundamental properties make cryogenic fluids difficult to store and transfer, and the process remains one of the greatest unanswered challenges of modern spaceflight.”
The refuelling system is only as durable as the weakest component. NASA is also planning similar “tools and technologies” for MRO in space, “satellite and spacecraft repair.”
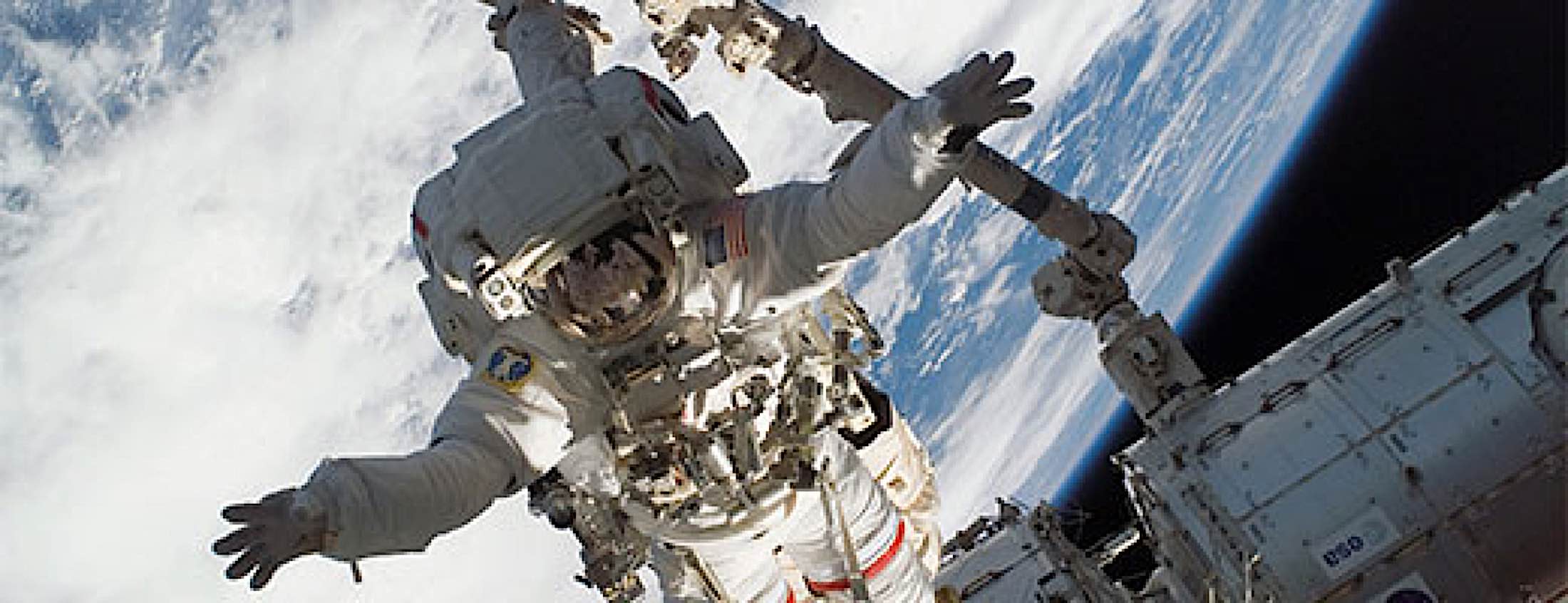
Canadarm
Canada’s robotic arm, Canadarm, became an icon of servicing and handling payloads in space, and served over 25 years in the space shuttle program, helped NASA maintain, repair and overhaul in space. Now, the Canadarm2 serves on board the International Space Station.
NOTES
[1] Pixalytics data according to the Index of Objects Launched into Outer Space, compiled by the United Nations Office for Outer Space Affairs (UNOOSA)
[2] Keeping Cool: Robotic Refueling Mission 3