Biodegradable materials are revolutionizing the world of additive manufacturing. Known for their ability to break down naturally, these materials are providing eco-friendly alternatives to traditional plastics and metals. This not only reduces waste but also aligns with global sustainability efforts.
Quick Facts
- Researchers are developing new biodegradable polymers for 3D printing applications.
- Biodegradable materials in 3D printing can be used for medical implants that should safely dissolve in the body.
- The use of biodegradable materials in additive manufacturing supports sustainable production practices.
- Biodegradable 3D printing filaments can be made from renewable resources like cornstarch.
- Additive manufacturing with biodegradable materials is gaining interest in the packaging industry.
- Biodegradable materials in 3D printing can help create eco-friendly prototypes and products.
- Advancements in biodegradable materials are expanding their mechanical properties for broader applications in additive manufacturing.
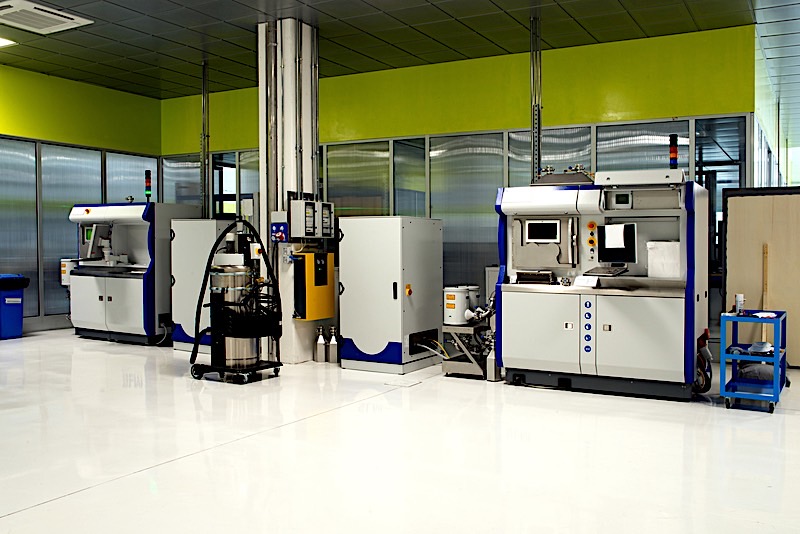
In recent years, the additive manufacturing industry has seen a significant rise in the use of biodegradable options. These materials, often derived from natural sources, decompose more easily in the environment, thus helping reduce the long-term impact of waste.
Biodegradable materials have some distinct advantages in additive manufacturing:
- Environmental Impact: They minimize pollution and reduce landfill requirements.
- Resource Efficiency: Often sourced from renewable resources, leading to a lower carbon footprint.
- Versatility: Suitable for various applications, from medical devices to packaging.
Quick Stats
- Approximately 8 million metric tons of plastic waste enter the oceans annually
- The use of biodegradable materials in 3D printing could reduce plastic waste by up to 30%
- Around 40% of 3D printing users are interested in sustainable materials
- The adoption rate of biodegradable materials in additive manufacturing has increased by 15% over the past three years
- Approximately 25% of 3D printed prototypes are now made with biodegradable materials
Developing Bio-Based Additive Materials
As the technology evolves, companies are continuously experimenting with new bio-based materials to enhance performance and durability while ensuring they remain biodegradable. This innovation is paving the way for more sustainable and responsible manufacturing methods.
Cost Efficiency and Market Trends
Biodegradable Material | Cost per Kilogram (USD) | Market Growth Rate (CAGR) | Environmental Impact |
---|---|---|---|
PLA (Polylactic Acid) | $20 | 25% | Low |
PHA (Polyhydroxyalkanoates) | $30 | 22% | Very Low |
Cellulose | $18 | 20% | Minimal |
Starch-based | $15 | 18% | Moderate |
Algae-based | $25 | 35% | Minimal |
The Science Behind Biodegradable 3D Printing Materials
Understanding how biodegradable materials function in 3D printing starts with the basics. These materials are commonly derived from natural resources like corn starch, sugarcane, and cellulose. The transformation from raw material to printable filament involves several advanced technological processes.
Firstly, the raw materials undergo fermentation and polymerization. During fermentation, microorganisms break down the natural resources into monomers. These monomers, such as lactic acid, are then chemically bonded into polymers in a process known as polymerization. This is where the bioplastics such as PLA (Polylactic Acid) are born.
The next step is crucial—processing these bioplastics into 3D printing filaments. This usually involves melting the polymer and extruding it through a nozzle to form continuous strands, which are then cooled and wound onto spools. The quality and consistency of these filaments are key, as they directly influence the printing process and the final product’s properties.
Adaptability of Materials
Another fascinating aspect is the adaptability of these materials. Manufacturers can tailor biodegradable polymers to meet specific requirements by altering their molecular structure. For instance, adjusting the ratio of different monomers can enhance properties like flexibility, strength, and melting temperature.
One might ask why conventional materials like PLA are popular in the biodegradable 3D printing sphere. The short answer: they offer a compelling balance of printability, structural integrity, and eco-friendliness. PLA is known for its ease of use, minimal warping during printing, and its capability to produce high-detail objects.
Non PLA Options
But PLA isn’t the only option. The industry is experimenting with other biodegradable polymers like PHA (Polyhydroxyalkanoates) and bio-composites, which blend natural fibers such as bamboo or hemp with bioplastics. These materials not only offer sustainability but also bring unique aesthetic and mechanical properties to the table.
Biodegradable 3D printing materials often come with an exciting promise—they can be decomposed back into natural elements. Under the right conditions, these materials can break down in industrial composting facilities, leaving behind no toxic residues.
In essence, the science behind biodegradable 3D printing materials marries the chemical wizardry of polymer science with the eco-conscious advances of modern technology. It’s a dynamic, evolving field aimed at reducing waste and promoting sustainability—all while pushing the boundaries of what’s possible with 3D printing.
Overcoming Limitations in Biodegradable Additives
One significant challenge with biodegradable additives is their mechanical properties. Often, biodegradable materials such as PLA (polylactic acid) cannot match the durability and flexibility of traditional plastics. To address this issue, researchers are continually developing composite materials that blend biodegradable polymers with natural fibers, such as flax or bamboo, to enhance strength and flexibility.
Another hurdle is the degradation rate of these materials. Some biodegradable substances degrade too quickly, which can be impractical for items that require longer lifespans. Innovations are underway to fine-tune the rate of decomposition, ensuring that materials remain functional for a desired period before breaking down.
Thermal stability is also a concern. Many bioplastics have a lower melting point, making them unsuitable for applications that involve high temperatures. Current research is exploring the combination of bioplastics with heat-resistant natural additives, aiming to extend their usability across a wider range of conditions.
The production cost of biodegradable materials, compared to conventional plastics, poses a considerable limitation. Economies of scale are not yet fully realized in the production of biodegradable raw materials, leading to higher costs. However, ongoing advancements in manufacturing processes and increased emphasis on sustainability are gradually driving prices down, making these materials more accessible.
By addressing these various limitations through continuous research and innovation, the integration of biodegradable additives in additive manufacturing holds promise for a more sustainable and environmentally friendly future.
Summary of the State of Biodegradable Materials in 3D additive manufacturing
- Increased Adoption: Leading companies are integrating biodegradable materials in their 3D printing processes, significantly reducing their carbon footprint.
- Material Innovation: Innovations such as biodegradable plastics and plant-based resins are becoming more prevalent, providing sustainable alternatives to traditional materials.
- Regulatory Support: Governments worldwide are promoting eco-friendly manufacturing practices, adding momentum to the adoption of biodegradable materials.
- Cost Reduction: Advances in technology are driving down the costs associated with biodegradable 3D printing materials, making them more accessible to a broader range of industries.
- Scientific Collaboration: Researchers and manufacturers are collaborating extensively, leading to breakthroughs that enhance the functionality and applicability of biodegradable materials.
- Education and Training: Increased focus on educating engineers and designers about the benefits and methods of using biodegradable materials is fostering a skilled workforce adept at green manufacturing.
- Consumer Demand: Growing consumer awareness and demand for environmentally friendly products are pushing companies to innovate and adopt biodegradable materials in their production processes.